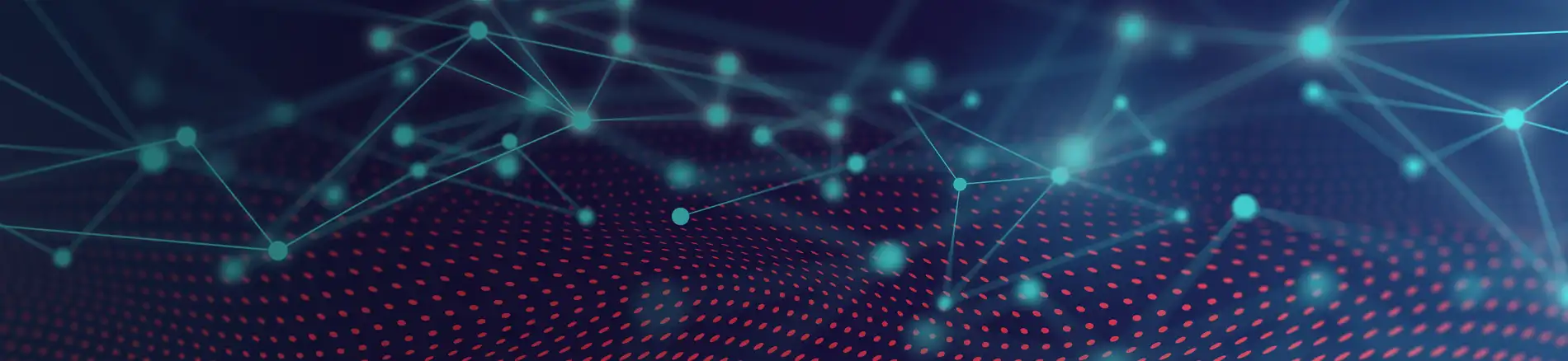

Drivers Of Demand Volatility – 3 Ways Supply Chains Can Respond
Supply chains are in the headlines every day, and they’ve never been more important to businesses, customers, and societies. As we continue to face a continuous chain of disruptions. The pandemic has further highlighted the need for both supply chain resiliency and customer-centric digital transformation.
Short-term fixes for supply challenges and flexible production to meet demand are only a temporary patch. So how can we help support supply chains to deliver resilient, hyper-personalised, sustainable products, services, and experiences?
In this blog we discuss these challenges with our core strategic partner SOTI.
Communication
From semi-conductor shortages, supply, and shipment issues at Christmas, to chip shortages and the Suez Canal blockages, and now rising fuel costs. It’s been a tough start to 2022 with constant supply chain disruptions in place. These disruptions identified the lack of communication up and down the supply chain and the heavy reliance on third parties. Which organisations now need to be tapped into. With 68% of customers saying that they expect to always know where their goods are in the delivery process, the expectations are set for effective communication and connectivity through the entire chain.
“To secure goods on time, customers are willing to pay up front, in full, and online. An exact delivery status and update expected. Customers will not accept an unclear or ambiguous reply and will shop elsewhere,” says Richard Gilliard, Managing Director at Renovotec.
“With all the mobile technology now available to organisations, with proven Mobile Device Management solutions such as SOTI MobiControl, communication can now be at the forefront. Notifications and issues with devices can be identified quickly and responded to remotely as if the device is in your hands. This means operations run smoother and communication lines are always live,” continues Faki Saadi, Director of Sales, France, Belgium and Luxembourg at SOTI.
Accurate forecasting
Most disruptions are not created inside the organisation – they are outside, and this is the challenge. The communication lines are not always open. And it is hard to have 100% visibility of the issues and where the chain weak points are. Being down in demand and then having to ramp back up – scaling is proving difficult for organisations. Especially with the great resignation and long covid impacts to operations and staffing. 57% of customers admit they have not been able to buy items or have had to source alternatives. With just 13% stating their retailer provides accurate information about their stock availability.
Predictability is hard and so is managing fluctuating demand. Once the silent partner in all the manufacturing and transport and logistics processes, the pandemic has now proven that supply chains are the life blood of any industry.
“Whatever the organisation, when companies evolve, the merging of technologies can be cumbersome and clunky. Getting the basics right is key; managing, securing, and locking down devices, as well as ensuring an easy-to-use mobility platform through which you can deploy applications, software updates and set notifications and alerts,” says Gilliard.
Keeping your warehouse stock inventory up to date starts with barcode scanners and mobile device platforms connecting devices. Without these there is no operation and no data on which to base your order history, and to be able to forecast recent trends and shipments.
Agility
Agility is essential in today’s modern world. Backup plans and being digital first are now essential modus operandi for any organisation. Customer’s must always be at the forefront to survive – and quick responses require agility to keep the supply chain moving. Planning is an ongoing process: how can you match supply and demand and inventory flow?
Handheld scanners are not reserved now for the warehouse, customers use them also and they need to be charged and ready to use. Battery power must remain high for the scanners to be used and for items to be ordered. A scanner failing due to a battery fault, or a poor network coverage will lead to a poor customer experience; frustration at wasting time and being unable to complete an order.
Recent SOTI research identified some interesting and eye-opening stats that will change the way your think about your supply chain and how it relates to customer experience:
- 68% of customers expect to know where their order is in the delivery process in real-time.
- 63% say great customer service is why they choose a brand.
- 61% prefer to shop with brands who can deliver goods the fastest.
Download the latest report here to find out more. Or click here to book yourself in for a chat with one of our mobility consultants.
Contact Us For Further Information.
Related Partner News
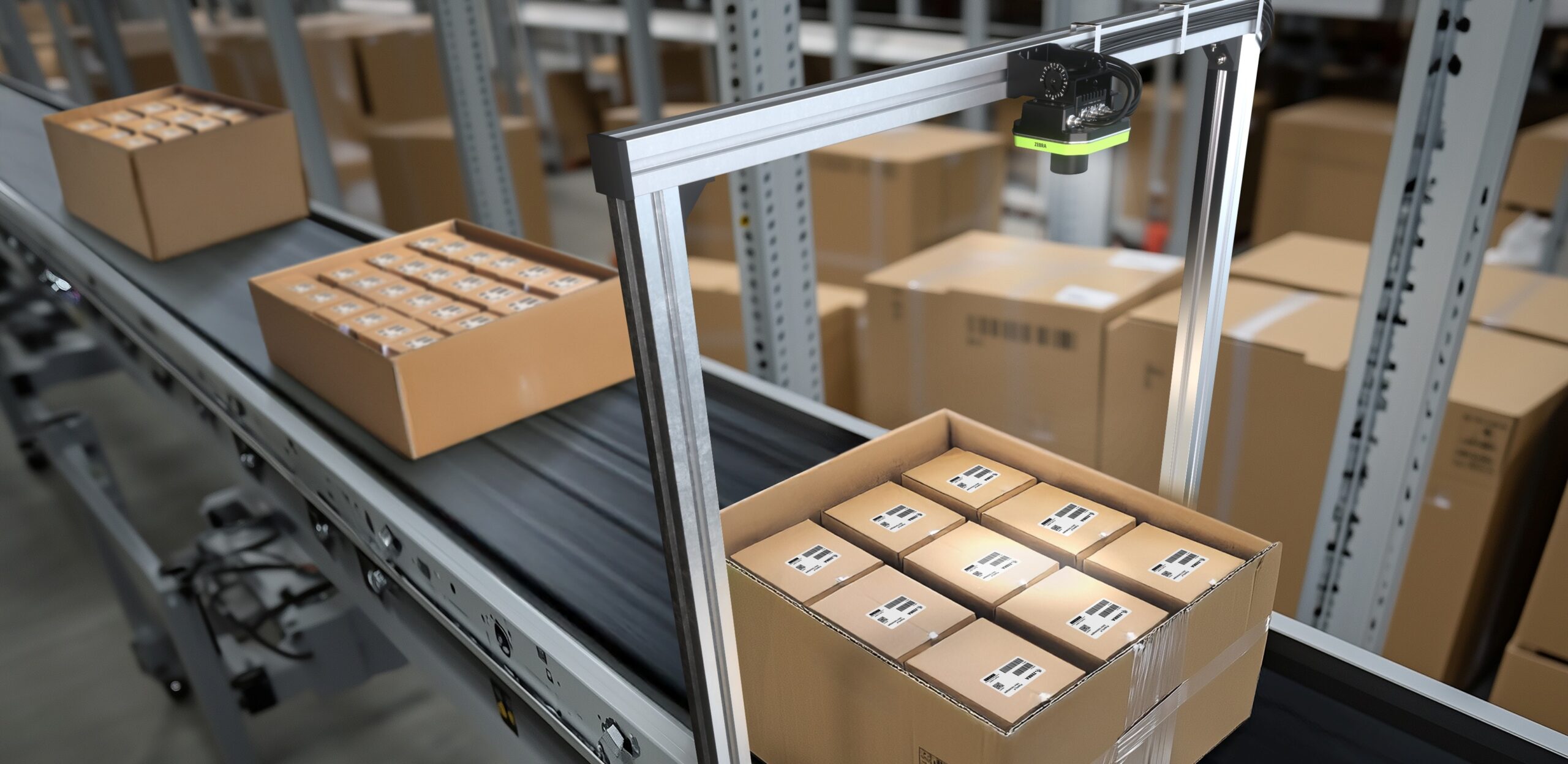
Accelerate Performance with Precision, Automation and Built-In Intelligence.
Built for Speed.
Designed for Accuracy.
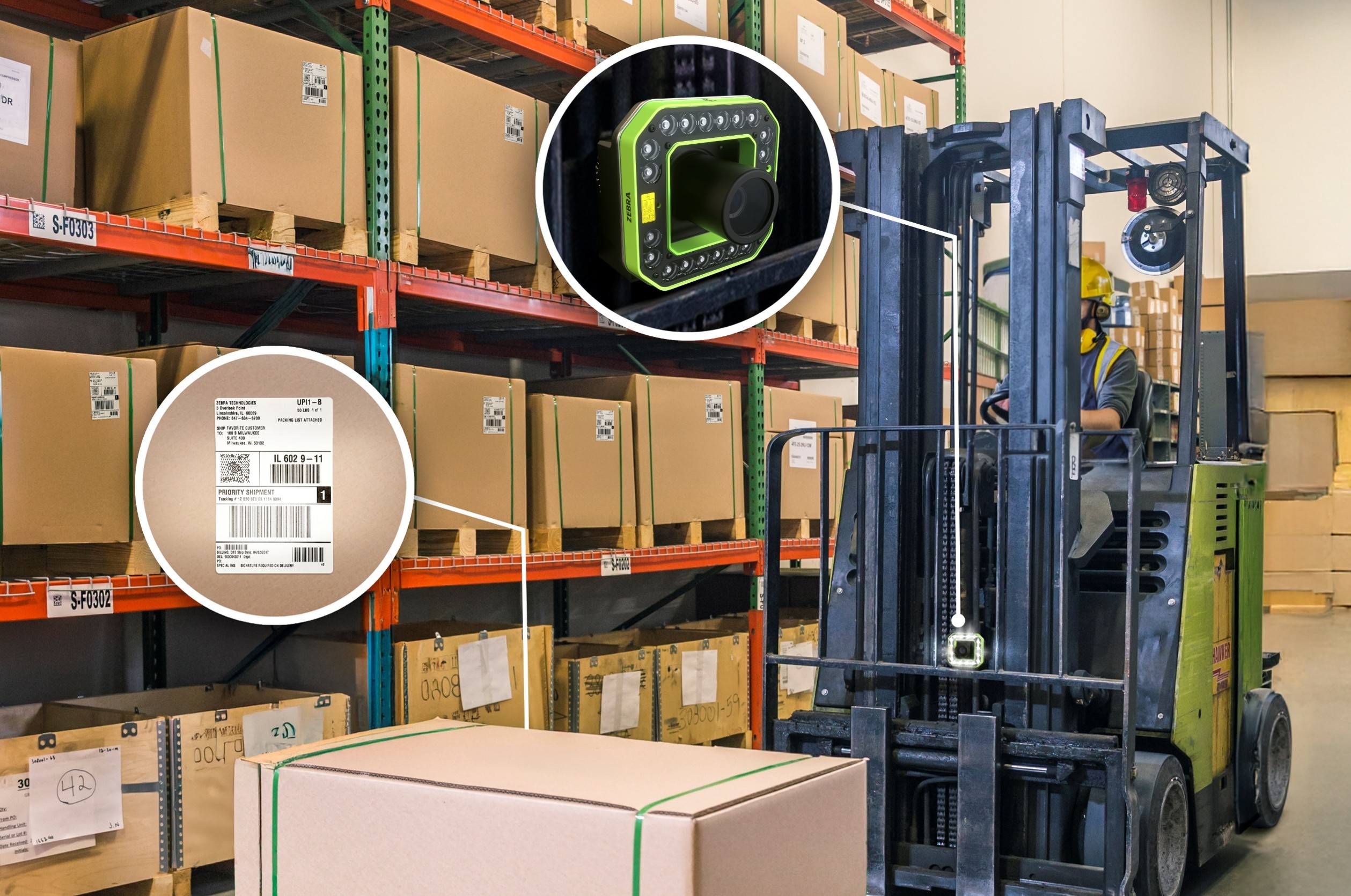
Transforming operations with fixed industrial scanners
Fixed industrial scanners are revolutionising the logistics sector, ensuring that products are shipped quickly and accurately to meet increasing customer demand, according to Jamie Mottershead, Technical Director at Renovotec.
Ecommerce is booming, with the sector experiencing continued growth, meaning distribution centres, warehouses, and supply chains need to process goods at a faster rate than ever […]
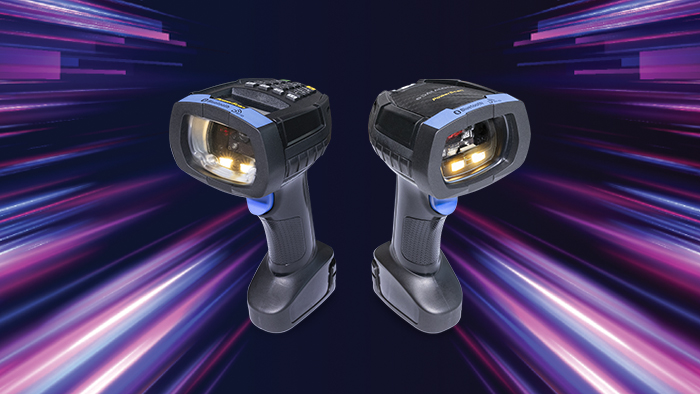
Datalogic PowerScan 9600 RFID Series, Built to do more
Datalogic is excited to introduce the PowerScan 9600 RFID Series, an industry-first hybrid device that integrates RFID and barcode reading in a single, rugged handheld unit.
This innovative scanner is designed to streamline operations across Retail, Transportation & Logistics (T&L), Manufacturing, and Healthcare.