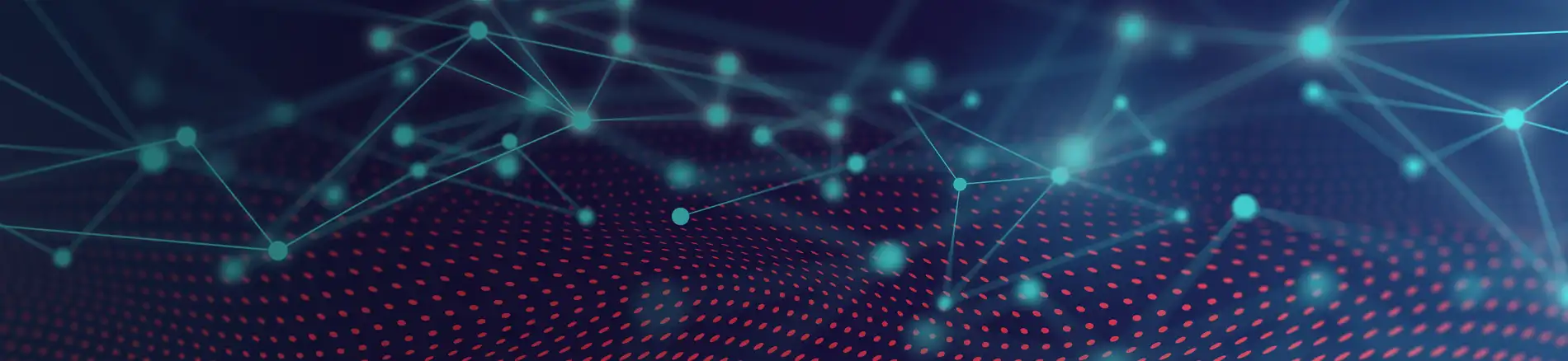
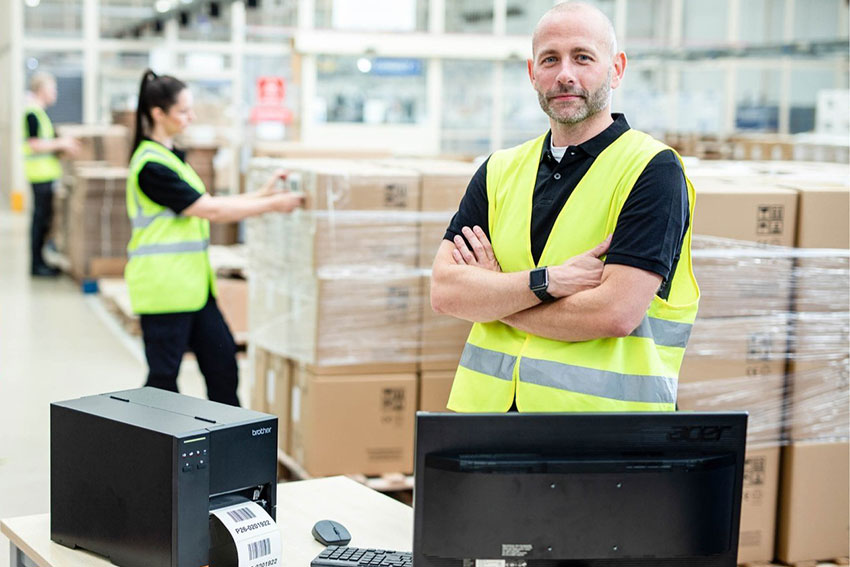
Hidden obstacles to warehouse efficiency: insights from Brother and Renovotec
With demand for e-commerce showing no signs of slowing down, and large warehouse rent costs rising by an average of 5% year on year*, the need for warehouse efficiency has reached a critical point in recent years.
Businesses have naturally turned to technology to streamline processes and cut costs. However, if the things that are hampering your workflow are difficult to identify, how can you choose the right technology to improve them?
That’s why in this blog, Brother and Renovotec have joined forces. To draw your attention to the hidden obstacles to warehouse efficiency – and share our thoughts on how to overcome them.
Spotlight on: inaccurate inventory counts
Product misplacement. Data entry mistakes. Labels that won’t scan. Inaccurate inventory information can happen for lots of reasons, but whatever the cause, the consequences can be serious.
From expensive overstocking and overordering, to understocking and unfulfilled orders disrupting the supply chain and leaving customers empty-handed, few businesses can afford errors in inventory counts in the current climate.
When ecommerce is so competitive, you only need to disappoint a customer once with an unfulfilled order, and that one lost sale could snowball into serious and widespread damage to your brand’s reputation.
So what’s the solution?
Many warehouse operators will look inwards to solve this issue: retraining staff, conducting frequent cycle counts in inventory management, and investing in RFID tracking labels.
However to maximise efficiency, it’s also important to look outwards, and consider the wider industry forces that are going on around you.
How does demand change throughout the year? Do you have access to timely and accurate information from manufacturers and retailers? Can you combine forecasting techniques with insights from your WMS to work out what seasonal inventory levels should look like?
Once you have this information at your fingertips, you can start rearranging products on the ground to match changes in demand. For instance, placing in-demand items in convenient locations (and at convenient heights) for easier picking, and a more efficient warehouse.
Spotlight on: Staff turnover
Speaking of wider industry forces: let’s talk about labour.
Widespread workforce shortages have been affecting all kinds of industries since the pandemic. However, warehouses have been particularly affected due to the relatively large labour force required, with labour costs accounting for around 65%** of a total warehouse budget (excluding shipping).
From pickers to administrators, even the proliferation of AI assistance has done little to dampen the recruitment crisis that is currently gripping the industry.
But this isn’t a hidden obstacle to warehouse efficiency: operators are painfully aware that they’re understaffed.
So what is? Well, it seems that while businesses have been panicking about getting more staff through the door, they’ve been forgetting about how to hold onto them once they’re in.
It’s an easy trap to fall into: being so worried about the impact of high training costs, high overtime costs, and costs to productivity and processing times, that you feel unable to invest in staff retention. But refuse at your peril: because low morale only results in high absenteeism, illness, errors and accidents – and ultimately a higher number of departures. Which will only add to the pressure on remaining employees, and cost your business more long-term.
So what’s the solution?
You can keep trying to recruit more staff, but it won’t solve the experiential problems you’ve got on the ground.
If you really want to boost efficiency, it’s time to invest in your existing teams, so your warehouse looks like a great place to work from both inside and out.
This might look like regular training programmes for all, not just new starters. Competitive wages, perks, and flexible work. Clear career progression opportunities, recognition for hard work, and policies that make your people feel valued.
It’s also worth thinking about automation. Now, warehouse employees might be naturally suspicious of robots taking their jobs. But when you invest in the kind of technology that simply makes their job less physically demanding – such as a portable label printer – the result is a more positive, more efficient environment for everyone.
Spotlight on: Accidents, thefts and product damage
Sometimes orders can’t be fulfilled due to issues with inventory counts. Sometimes, there aren’t enough staff to fulfil them. And sometimes the stock just gets broken or, sadly, stolen.
One major consequence of the rise in next and same-day deliveries is that goods must move faster than ever before. Boxes of product are repeatedly picked up and dropped by increasingly rushed workers, and even if the professionals handle with care, there’s no guarantee that customers returning their orders will.
The results are inventory shrinkage, higher insurance rates, and even the risk of injury to staff. Plus the time and money wasted by re-handling, re-packaging, or disposing of goods. All of which can significantly erode profit margins.
So what’s the solution?
Improving employee morale, as we mentioned above, will go some way towards preventing thefts and lack of care leading to accidents. You can also improve ergonomics and safety controls to help protect your people, products, and by extension, profits.
It’s also important to reconsider the basics: things like insurance policies, and screening and training new employees.
You could think about advanced surveillance systems such as CCTV and night vision cameras, or AI-powered analytics to detect unusual patterns of employee behaviour. But tread carefully, as obvious declarations of distrust could backfire in terms of staff retention.
RFID technology is a great compromise, as it helps you keep a closer eye on your inventory, without staff feeling accused. An efficient way to handle an insidious problem.
Spotlight on: Labelling hardware that isn’t fit for purpose
There’s a reason that RFID labels keep popping up as solutions to hidden warehouse obstacles, and it’s because labels are one of the most important things for keeping warehouses moving.
So when the labelling hardware isn’t up to scratch, efficiency naturally drops. In one survey, 57%*** of reported warehouse inefficiencies were caused by labels that couldn’t be properly scanned, due to poor-quality printouts and smudged barcodes. Issues like this lead to costly errors in picking, packing and inventory counts, while frequent breakdowns and paper jams slow down processes and increase maintenance costs.
So what’s the solution?
Reconsider your label printing solution.
Are staff wasting time going back and forward to a desktop label printer, when they could be using a portable one?
Are they trained in how to manage printing errors or maintenance issues, or if not, is there someone on every team who is?
Are you confident that your current label printing hardware genuinely meets the needs of a fast-paced warehouse in today’s climate?
When you work closely with label printing experts, issues like this can be ironed out easily. In fact, from tighter control over your inventory to an easier life for your team, you might be surprised by just how many hidden obstacles to warehouse efficiency can be overcome in the process.
Take Brother and Renovotec’s free warehouse printing assessment now, and find out how small changes to your label printing setup could transform efficiency for your business.
* Source: Industrial & Logistics Rents Maps H2 2024, Colliers
** Source: Managing Warehouse Labor To Reduce Expenses, Penske Logistics
*** Source: How Clever Solutions Could Transform Your Warehouse Labelling Process, Brother.
Related Partner News
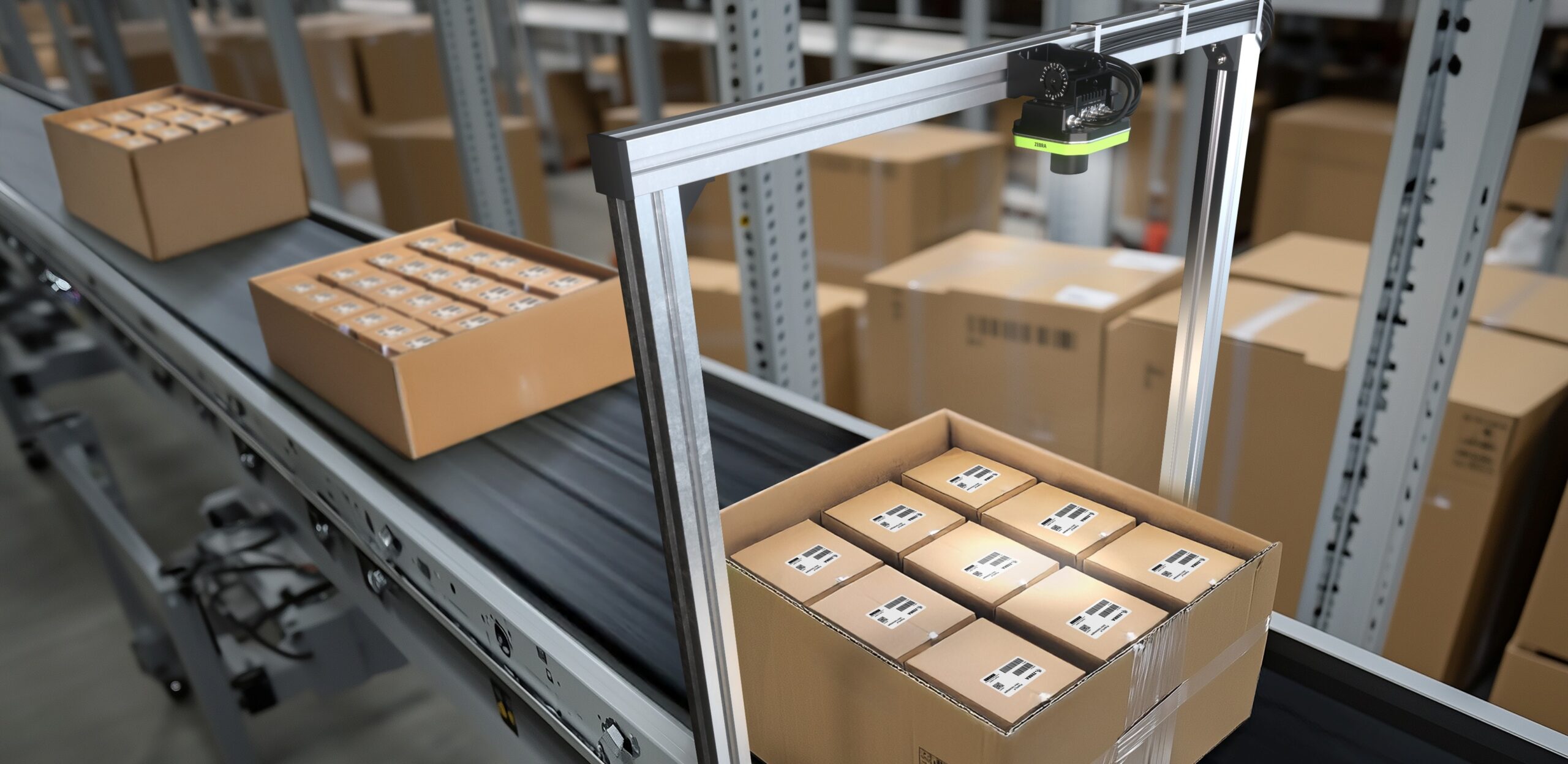
Accelerate Performance with Precision, Automation and Built-In Intelligence.
Built for Speed.
Designed for Accuracy.
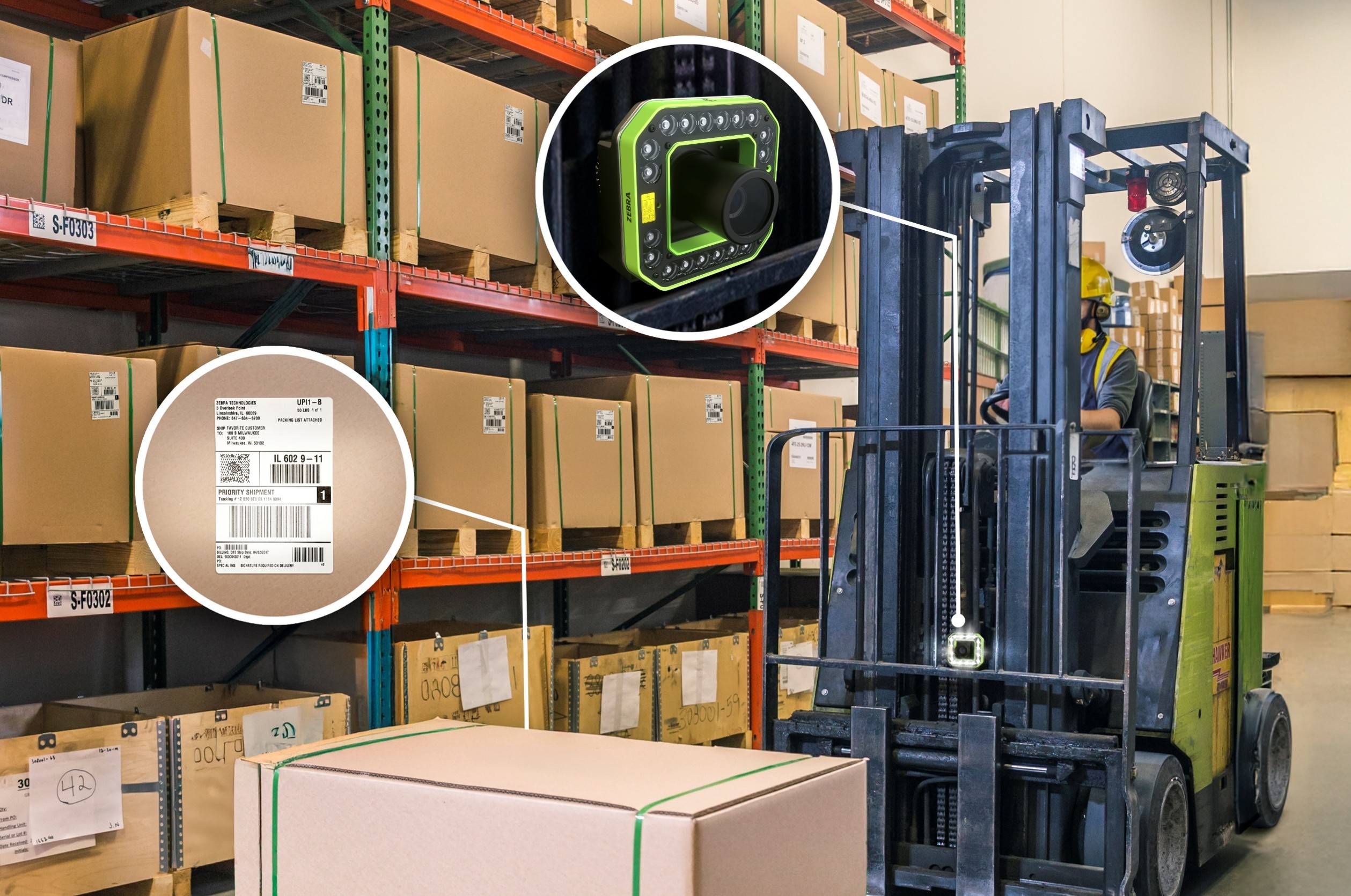
Transforming operations with fixed industrial scanners
Fixed industrial scanners are revolutionising the logistics sector, ensuring that products are shipped quickly and accurately to meet increasing customer demand, according to Jamie Mottershead, Technical Director at Renovotec.
Ecommerce is booming, with the sector experiencing continued growth, meaning distribution centres, warehouses, and supply chains need to process goods at a faster rate than ever […]
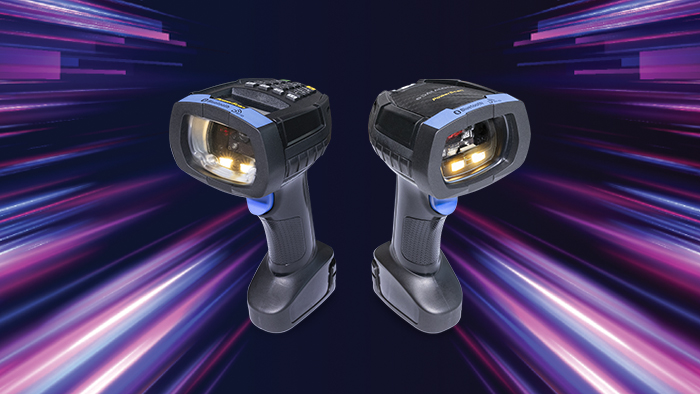
Datalogic PowerScan 9600 RFID Series, Built to do more
Datalogic is excited to introduce the PowerScan 9600 RFID Series, an industry-first hybrid device that integrates RFID and barcode reading in a single, rugged handheld unit.
This innovative scanner is designed to streamline operations across Retail, Transportation & Logistics (T&L), Manufacturing, and Healthcare.