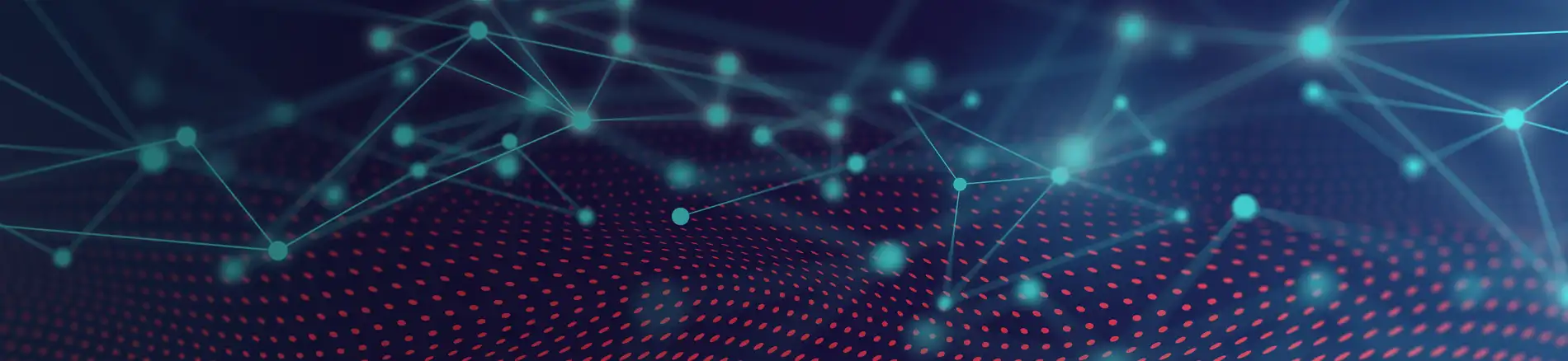

Increase Efficiency With Cold Storage Automation Solutions
How cold storage automation solutions can enhance your supply chain operations…
The continued growth and development of computer technology is an inevitable influence on every industry, and cold storage is no exception.
Consumer safety is the primary role of cold chain management. With the dramatic increases in consumer grocery demands and pharmaceutical products over the past few years, maintaining productivity levels, and keeping your workforce safe, there has been no shortage of challenges for cold chain storage facilities.
Now that automation is readily available and supply chain disruptions are likely to continue in the near future, cold chain automation becomes more of a “need to have” rather than something that is just nice to have.
The first and foremost goal of automation within this arena, is to reduce inefficiencies in operations and to ensure consumer safety. Additionally, the surge of e-commerce and the numerous disruptions throughout the past year has encouraged companies to speed up their investments in warehouse automation and automation systems to reduce inefficiencies, help build resiliency and protect against further disruptions.
With margins tight and employee resources scarce, particularly coming out of the pandemic and with Brexit visa issues, having the ability to let technology handle manual, tedious tasks is the key to success and in some cases, even survival.
What are the main advantages of cold storage automation?
With the implementation of automated storage systems and handling equipment, companies with cold storage warehouses will realise the following benefits:
- Increased productivity: in freezing environments, only automation guarantees high-frequency inflow and outflow cycles. This is because the excessive exposure of operators to these temperatures can be detrimental to their health.
- More efficient order prep: the deployment of automatic or semi-automatic picking systems — for instance, voice-picking and pick-to-light — shortens the time operators spend in the cold rooms, optimising their picking routes and boosting efficiency in order prep.
- Improved safety and hygiene: automated cold storage warehouses see to it that both the products and the employees are protected, reducing goods management errors and preventing operators from exposure to extreme environmental conditions. Plus, automation ensures hygiene in all logistics processes, a key factor in sectors such as the food and pharmaceutical industries.
- Logistics cost savings: energy is the most valuable asset in cold storage. Automated solutions maximise the volume of the facilities, lowering the energy consumption per pallet.
- Warehouse space optimisation: solutions such as the Pallet Shuttle help to condense storage space, eliminating aisles in the building.
- Long-term storage of frozen foods and other consumer products is one of the biggest challenges in the cold storage supply chain. Not only is this phase also prone to human error, but it requires extra attention due to the time-sensitive nature of frozen goods.
How is cold storage automation enhancing workflows?
As well as the grocery industry, other industries also depend on cold storage. The medical industry uses cold storage to facilitate drug testing and storage, mixing specific ingredients and handling human tissues before surgery. Many manufacturers – including those in automotive, clothing and metalworking – test or store their goods at low temperatures to ensure durability, longevity and freshness.
Once again, automation has the potential to save the day. By automating processes like stock rotation, warehouses can ensure that they’re always distributing fresh items. RFID chips and scanners provide a way of tracking expiration dates, too, and automated picking systems can locate these expired goods for separation and eventual disposal.
Streamlining a warehouse layout and reducing floor space is just the start of things to come with the increase of cold storage automation. By using innovations like data analytics and the IoT in tandem with automation, manufacturers can reduce their long-term storage needs altogether. By accurately forecasting consumer habits, staging expected orders and capitalising on recent trends, it’s possible to elevate the supply chain – and, by extension, the customer experience – to brand new heights.
Working in extreme temperature conditions requires specialised mobile devices that can operate in cooler, chiller or freezer environments. Which means equipment must be able to handle not only cold temperatures but, in many situations, constant movement between different temperature zones and changing levels of humidity. Honeywell have an extensive portfolio of products that are specifically made for cold store that can streamline processes, increase accuracy and ensure safety.
The portfolio includes:
- Rugged mobile computers, tablets, vehicle-mount computers and wearables for cold /freezing environments.
- Ultra-rugged handheld scanners that enhance order accuracy and speed shipping times in demanding harsh environments.
- Durable, easy-to-use industrial and mobile printers with certified supplies that offer the latest connectivity interface with your mobile computers to bring high-quality printing and label application right into your cold storage supply chain.
In Summary
The cold chain is a harsh, demanding environment. Cold storage distribution requires extreme conditions as rigid as -30°C (-22°F) to much warmer areas – up to 50°C (122°F) – and back again. This needs to be achieved without a drop in performance or productivity within the workflows.
Utilising refrigerator- and freezer-compliant mobile devices and networks that can withstand low temperatures and condensation improves traceability capabilities, enhances order accuracy and speeds shipping times in cold storage environments. With reliable operation, regardless of the dramatic temperature swings, workers can quickly and efficiently enter data – even with gloved hands – by using large keys and an easy-to-use touchscreen on ergonomically designed handheld mobile computers.
Find out how Renovotec & Honeywell can solve all your points of pain with our cold storage supply chain solutions.
Related Partner News
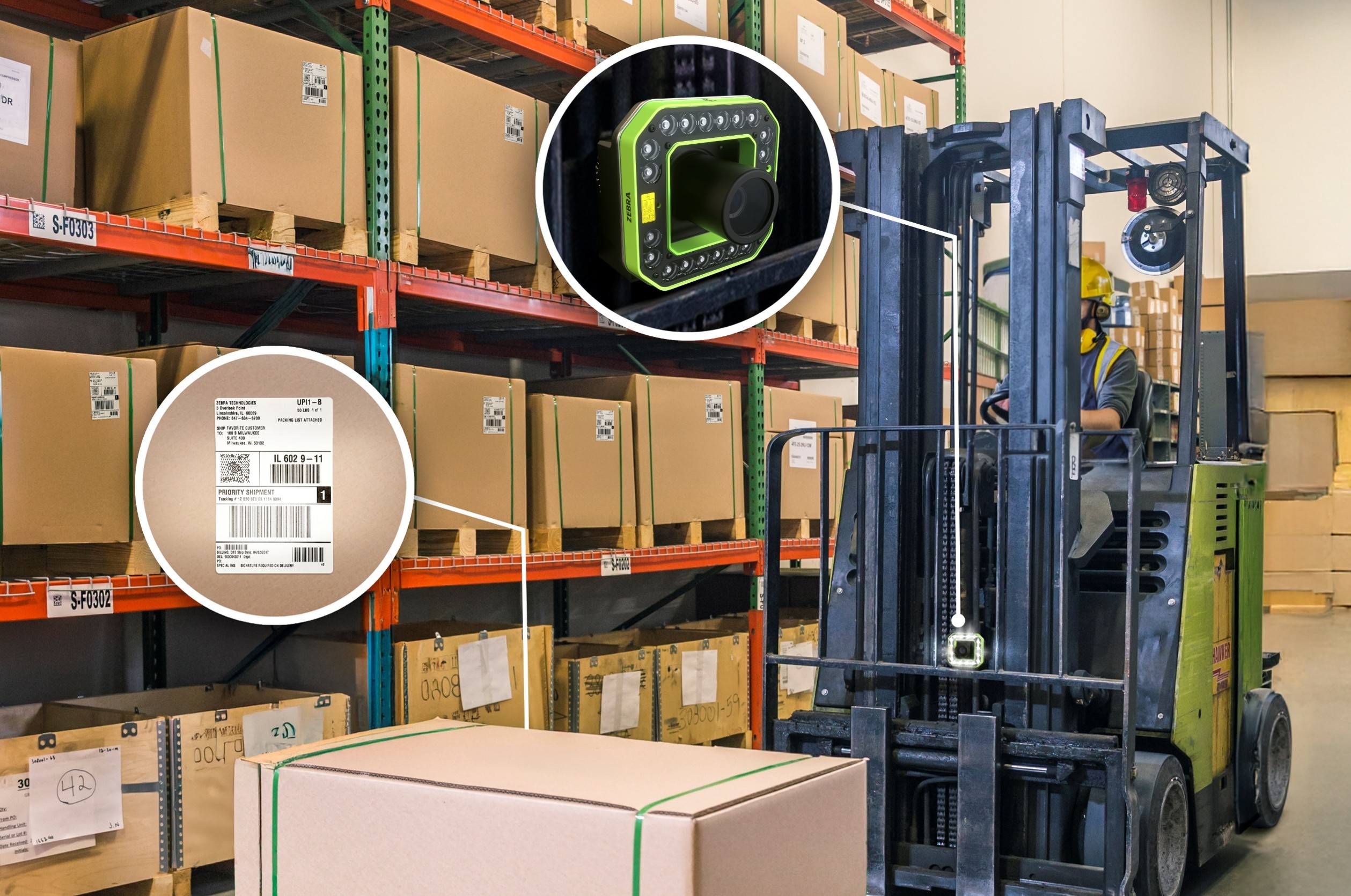
Transforming operations with fixed industrial scanners
Fixed industrial scanners are revolutionising the logistics sector, ensuring that products are shipped quickly and accurately to meet increasing customer demand, according to Jamie Mottershead, Technical Director at Renovotec.
Ecommerce is booming, with the sector experiencing continued growth, meaning distribution centres, warehouses, and supply chains need to process goods at a faster rate than ever […]
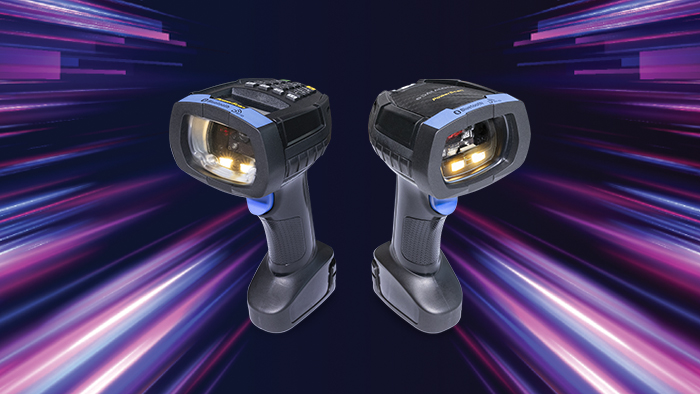
Datalogic PowerScan 9600 RFID Series, Built to do more
Datalogic is excited to introduce the PowerScan 9600 RFID Series, an industry-first hybrid device that integrates RFID and barcode reading in a single, rugged handheld unit.
This innovative scanner is designed to streamline operations across Retail, Transportation & Logistics (T&L), Manufacturing, and Healthcare.
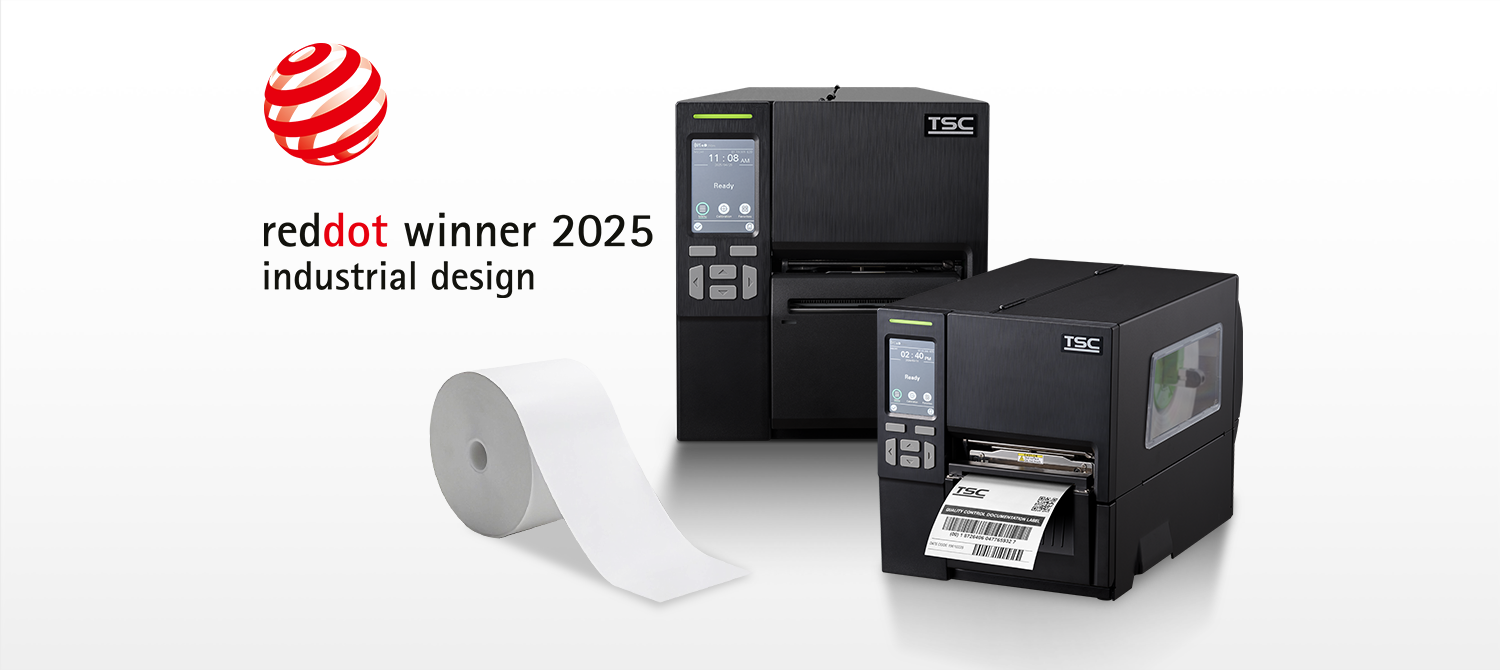
TSC Auto ID MB241 Series Linerless Printer Wins Red Dot Award
TSC Auto ID, a global leader in automatic identification and data capture (AIDC) and thermal label printing technologies, have announced that the MB241 Series linerless printer has been recognised for design excellence with a Red Dot Award: Product Design 2025 in the Industrial Equipment, Machinery, and Automation category.
“We are thrilled the MB241 Series linerless […]