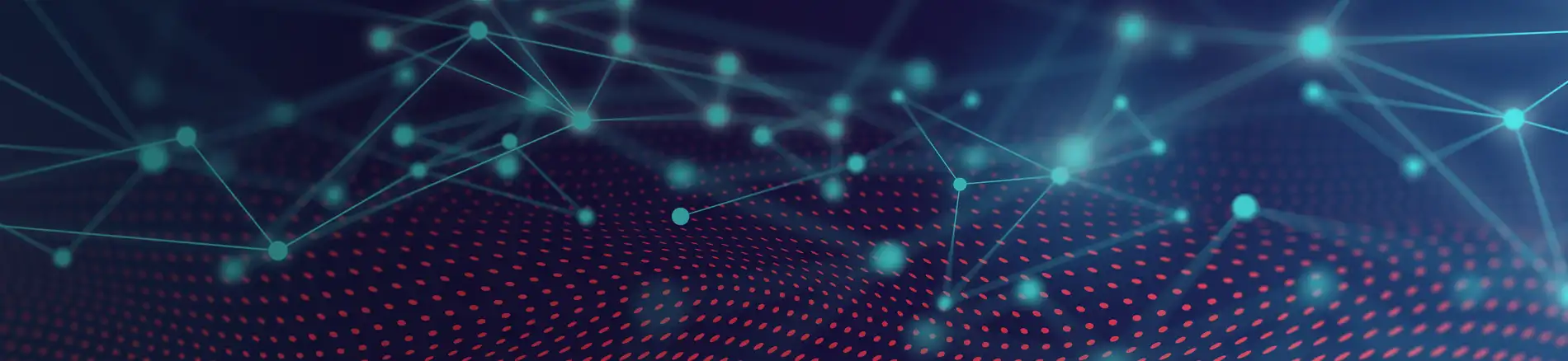
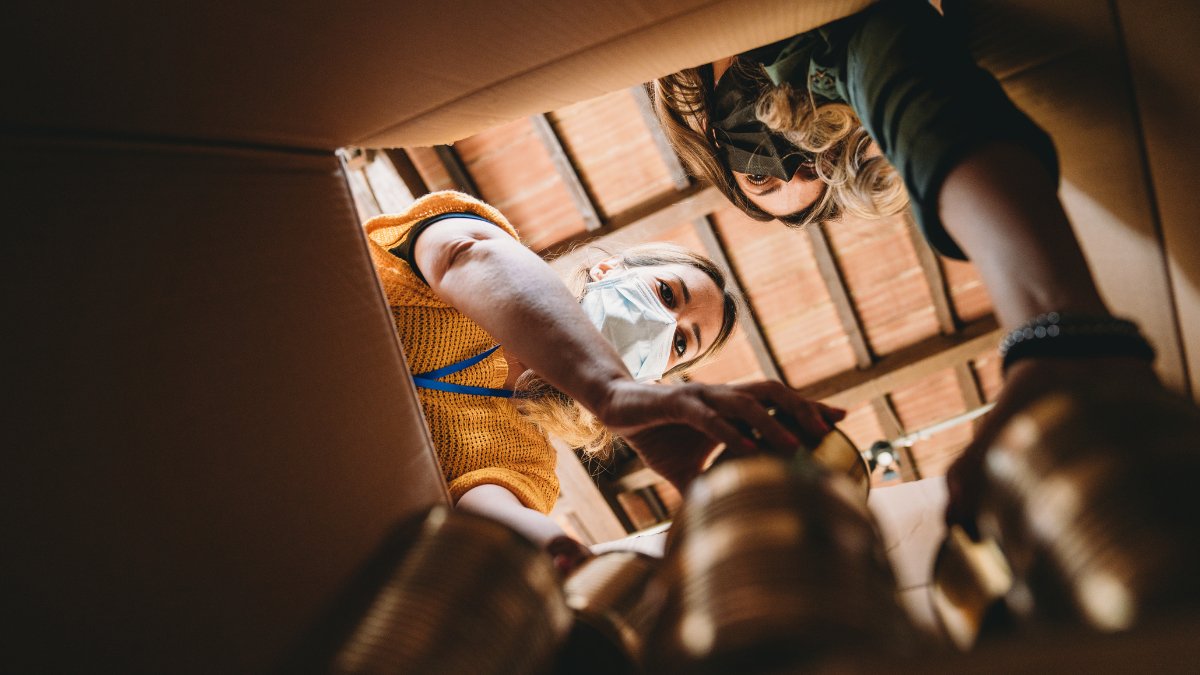
6 Ways to Improve Warehouse Efficiency with a Packing Bench Solution
How can a packing bench solution revolutionise the efficiency of your warehouse processes?
Ensuring your warehouse operations are optimised is essential if you want to succeed in today’s highly competitive e-commerce market.
Warehouses and order fulfilment centres are increasingly adopting cutting-edge technology solutions such robotics and AI to help ensure orders are fulfilled faster and more efficiently. A packing bench solution is one such tactic for truly streamlining the efficiency of your fulfilment operations.
An enhanced packing bench solution is one such option. It frees up your resources and helps boost the operational efficiency of your business.
Today, we’d like to share what packing bench solutions are and why they’re a vital component to the growth of your warehouse operations.
What is a packing bench solution?
A packing bench solution combines robust tools and best-of-breed innovations in data collection, print and software to streamline the packing process. This includes packing selected items, printing delivery labels and sealing the boxed order, ready for loading.
A typical solution like this usually includes:
- A robust bench
- An overhead scanner
- A label printer
- A handheld scanner (optional)
- Software to manage the process, usually integrated into the WMS
This allows for streamlined warehouse operations, faster order fulfilment and better customer satisfaction. Here at Renovotec, we work with a carefully curated ecosystem of trusted partners to ensure every component delivers exactly what your business needs.
Visit this page to see a warehouse packing bench in action.
What are the benefits of using packing bench solutions from Renovotec?
Using an enhanced packing bench solution is the forward-thinking choice for any business that wants to compete in the highly competitive e-commerce market. Here are six reasons why these packing bench solutions can be a game-changer for your business.
1. They improve order accuracy
When you adopt a packing bench solution, you’ll benefit from a centralised workspace with everything your team member needs to ensure accurate and speedy order fulfilment.
You can reduce human errors by streamlining the workflow, utilising hardware and software that seamlessly integrates with your existing WMS.
As a result, your customers will feel more satisfied with the service and are more likely to leave positive reviews, recommend you to friends and family and return with new business.
2. They ensure faster packing times per order
Packing bench solutions often utilise a fixed scanning element, such as an overhead scanner that can read even partially obscured logos with high accuracy. This reduces the overall time spent completing each order, making this area of the warehouse more cost-effective to run.
With everything in one workstation, team members will spend less time moving between packing stations and tools. Then customise these technologies to meet the unique branding and system-related requirements of your business.
3. They allow you to re-allocate staff resources elsewhere
Implementing a this technology means you can free up valuable staff resources that can be used elsewhere.
Team members have all the tools and information they need to perform their function from one location. This increases their overall productivity and enables you to redistribute staffing resources to other areas of the business.
4. They ensure stricter policy and procedure compliance
Warehouses must adhere to specific policies and procedures to ensure regulatory compliance, quality control and health and safety standards are met.
When you adopt a packing bench solution, existing workflows can be integrated into the system and can guide workers through the process. This ensures strict compliance and adherence to policies and procedures. It also protects quality, reduces errors, and helps you ensure company standards and compliances are consistently being met.
5. They can scale with your growing operations
Scale a packing bench solution to match the evolving needs of your business and can grow alongside you business. As your fulfilment operations scale up, this element of the process can easily scale with it.
A packing bench solution results in seamless business expansion without disrupting the existing workflow and ensuring customer satisfaction, every step of the way.
6. They enhance customer satisfaction
Customer satisfaction is key when it comes to ensuring profitability and growth. Protect the customer experience thanks to shorter processing times and few overall errors.
This means less misprinted or misplaced labels and less missed items in an order. With a reduced lead time thanks to the speed of using an overhead scanner, a packing bench solution ensures your customers are receiving their goods as part of streamlined and efficient service.
Summary
If you’re looking to optimise your warehouse operations, a packing bench solution is the answer you’ve been looking for. Leverage improved order accuracy, reduced packing time, enhanced customer satisfaction and much more.
Hands-free scanning with an overhead scanner speeds up the data collection process, enabling you to automatically print a label with correct information drawn from your own secure WMS. With a carefully selected array of technologies and tools, this solution gives your staff the tools to perform at their best.
Discover packing bench solutions and more at our new Renovotec Innovation Centre (RIC)
Did you know that we have opened our brand new Renovotec Innovation Centre (RIC) near Warrington?
Visit us to get hands-on experience with these innovative technologies, including our packing bench solutions.
Enjoy interactive demos and meet our technology experts to learn more about these. Contact one of our experts today to learn more.
Related Blog Posts
Retail Experts Share Top E-Commerce and Logistics Trends for 2025
Faki Saadi, Director of Sales UKI at SOTI and Richard Gilliard, Managing Director at Renovotec, explore the key trends shaping the future of the retail supply chain From Asda rolling out electronic shelf labels to Amazon launching ‘Prime Air’ a delivery drone service, retail brands are evolving and looking to the latest technologies to keep […]
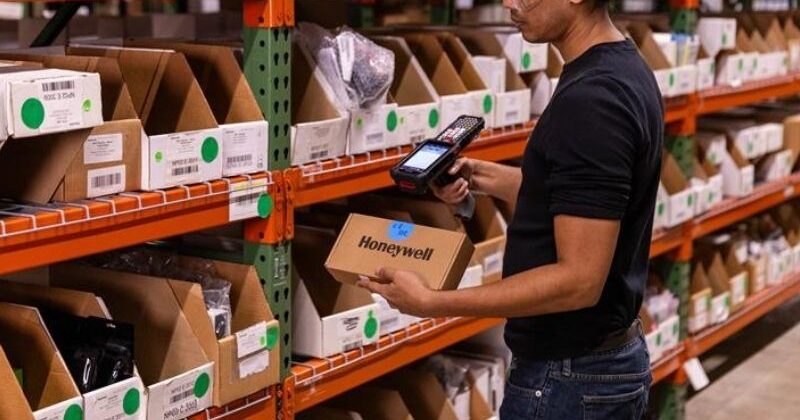
Upgrading the supply chain with Honeywell voice and mobility solutions
How can you transform your supply chain operations and ensure competitiveness in the market with voice and mobility solutions from Renovotec and Honeywell?
Improving productivity and efficiency gains are vital for the profitability of businesses in the supply chain.
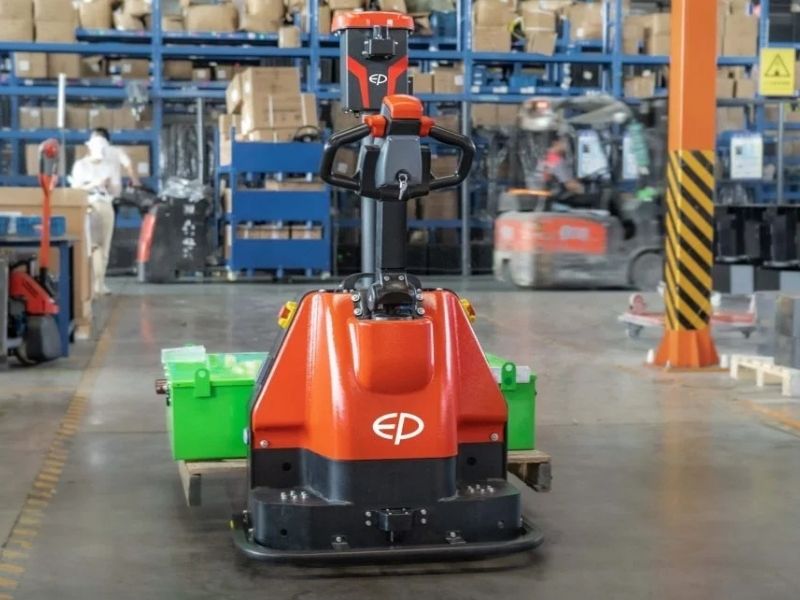
Autonomous pallet trucks: smart material handling technology
Autonomous pallet trucks are introducing a range of new capabilities for the supply chain… Transporting goods and materials is a key part of the supply chain.
This includes storage, order fulfilment and other processes.