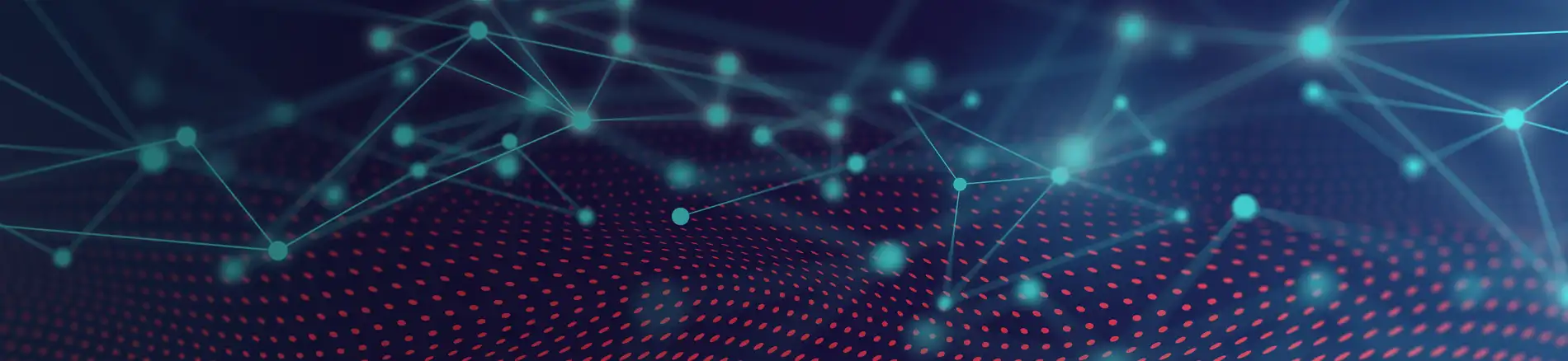
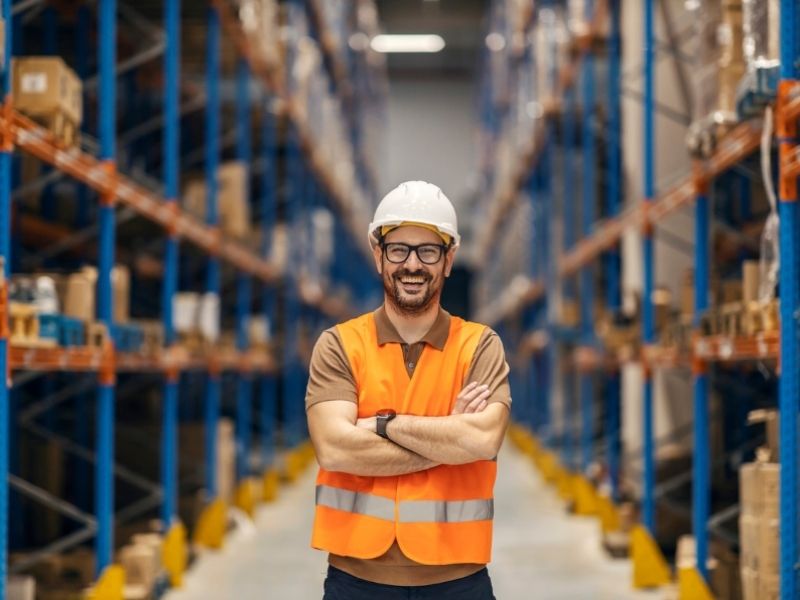
Automation Helps Remove The Guesswork For Manufacturing Plants & DCs
How can automation in manufacturing plants and DCs enhance operations?
You can’t switch on the TV or read newspapers without seeing reports of stocks running low of anything from Christmas toys to essential food items. Indeed, I read in one national newspaper that two-thirds of shoppers are either worried or very worried about potential food and drink shortages in the run up to Christmas.
Inaccurate inventory management lies at the heart of many supply issues. As few manual or paper-based methods are up to the job. To be fully functional, an inventory system needs complete visibility of its supply chain for tracking and viewing in real-time. More traditional approaches don’t deliver this level of transparency. So manufacturers and retailers are left guessing how much inventory is available or in transit.
Having up to date data allows businesses to adapt with far less headaches. Especially in desperate situations like we’ve been seeing recently. Knowing where your goods and raw materials are, and the condition they’re in, at each point of the chain is key to successful supply chain management.
Real-time inventory visibility can also eliminate the dreaded ‘out of stocks’ (OSS). As some 80%1 of retail executives agree they need better inventory management tools to check accuracy and availability. Retail OSS is said to cost $190.1billion* in the EMEA region.
Benefits of automation in manufacturing plants and DCs
With the meteoric rise of ecommerce and on-demand logistics, keeping track of things by physically counting them and updating spreadsheets is no longer practical. Automated inventory management and tracking solutions make it easier for manufacturers and retailers to:
- Better predict demand.
- Lessen human error.
- Inform business decisions through better reporting.
- Remove inefficiencies and save time.
- Reduce manual process cost and increase productivity.
Through software, mobile devices like computers and scanners, and RFID tags, you can gain the visibility you need. By 2024, use of RFID and location technology are expected to increase. As one in five† respondents in Europe plan to use them for inventory management (20%).
Improving workflows
One of the major issues in distribution centre workflows is reducing ‘dock to stock cycle time’. Especially noticeable with more paper-based processes. Using mobile devices with advanced imaging technology is 25% more productive and 50% more accurate than paper or manual methods. Which shows what can be achieved through efficient, real-time inventory management. Honeywell’s Dolphin CK65 mobile computer, for example, not only improves inventory accuracy and order cycle time. But also maximises worker productivity. What’s more, it’s a future-proof investment with support for four Android generations. Starting with Android 8(0).
According to Honeywell, the average number of unproductive minutes per 8-hour day, per worker in distribution centres is 22. Whether it’s using mobile printers to put stock away or use handheld scanners to cycle count, you increasingly need automated inventory management for easier and better worker productivity.
Advances in technology have revolutionised supply chains and manufacturing plants in recent years. Inventory management may not seem an investment priority but it sure the hell is important and removes guesswork from the equation. Automating it will make it easier for you to control inventory based on demand, it will improve your overall results and reduce costs.
*Source: https://www.ihlservices.com/news/analyst-corner/2018/06/worldwide-costs-of-retail-out-of-stocks/
Related Press Releases

Renovotec Expands Global Footprint with Two New Offices
Fast growing AIDC provider responds to customer demand Warrington, UK – 9am BST, 24th October: Renovotec, the UK’s fastest growing provider of end-to-end automatic identification and data collection (AIDC) technology solutions and services for organisations operating throughout the supply chain, today announced the strategically significant opening of two new offices, one serving the Nordic region […]
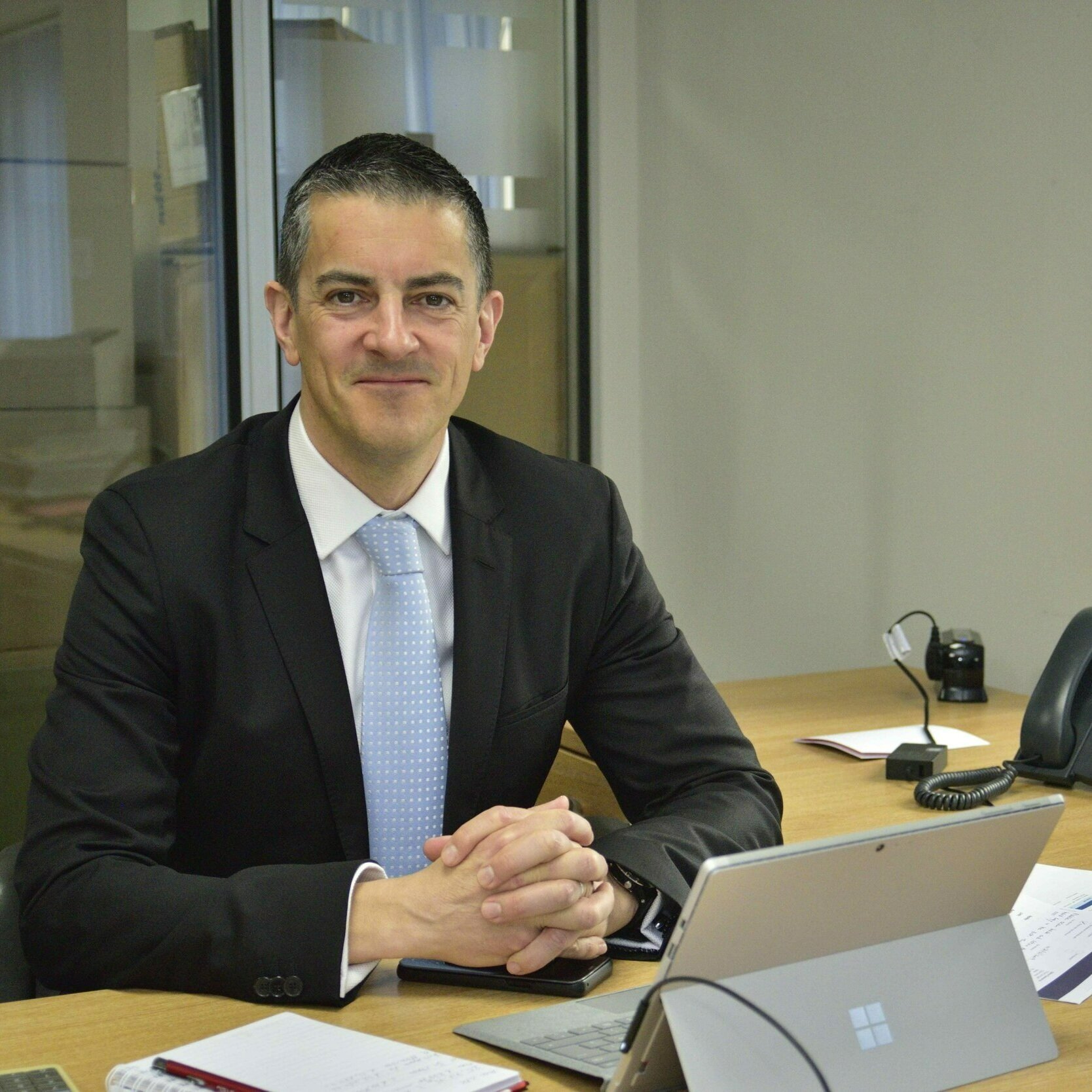
Renovotec Launches Printer Audit Scheme
Supply chain solutions and services company Renovotec is launching a free three-month trial for its printer audit service, the company announced today.
The audit helps a supply chain company to understand its printer estate.
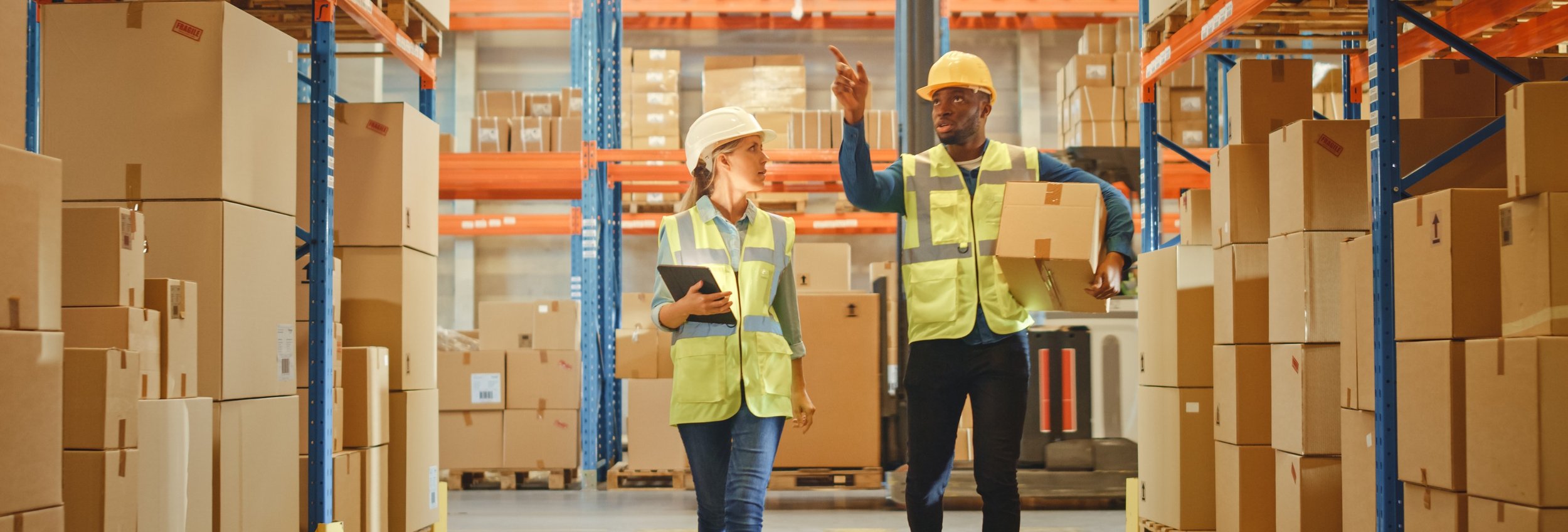
Three Considerations for Warehouse Expansion and How They Impact Productivity
Omnichannel is Driving Warehouse Expansion.
With an expansion of retail omnichannel experiences, some of the world’s largest retailers are spotting further opportunities for growth by acquisition.