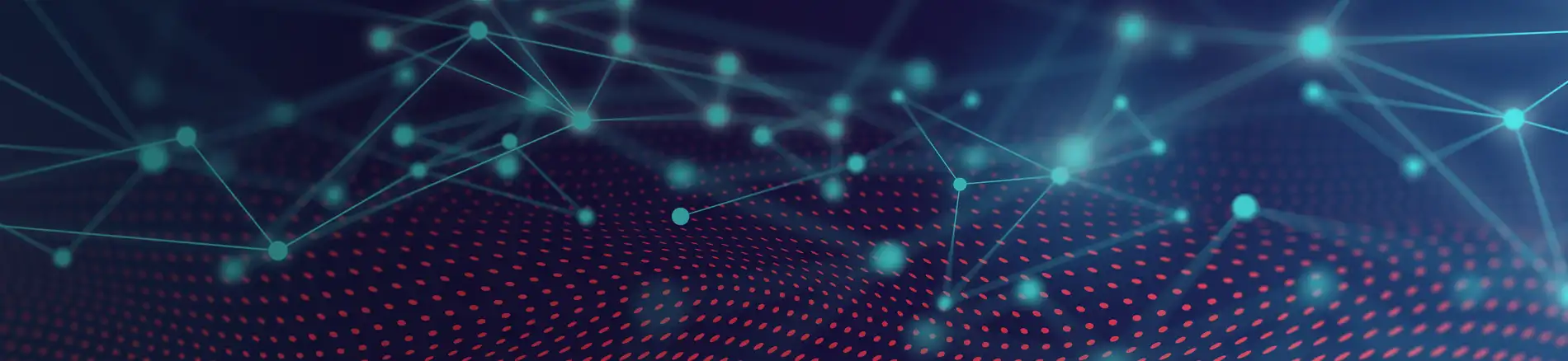

Voice Quiz – Is voice automation a solution for your operation?
Can voice automation enable your distribution centre (DC) to meet ever increasing requirements for omnichannel fulfilment while enhancing accuracy, productivity and profitability?
Picking remains among the most labour-intensive supply chain operations. It’s also one of the DC processes that can be improved with voice technology.
Answer the six questions below to determine whether voice-directed workflows are the right choice for your operation.
Download White Paper – ROI of Voice Picking.
Contact us for further information & pricing.
Explore 5 Ways Voice Automation Positively Impacts Picking Workflows.
1. Do your existing manual picking processes increase costs and delay order fulfilment and delivery because of picking errors?
Voice-automated picking improves accuracy rates to nearly 100% by enabling workers to focus on the task at hand.
Errors in the picking process can cost anywhere from £10 to £250 each, depending on the value of goods and processing costs. Incorrect or incomplete orders spoil the customer experience; erroneous deliveries to retail outlets become lost revenue or returns that have to be sold at a discount. These hidden costs can quickly add up, but companies that utilise voice technology can minimise or avoid picking errors altogether.
2. Do employees spend too much time handling paper order forms and finding the right pick locations?
Voice-guided workflows provide workers with pick instructions and specific item locations; workers listen and respond with confirmations. Streamline movement throughout the DC by eliminating routes, minimising steps, and enabling your employees to work hands-free and eyes-up. This can result in productivity improvements up to:
35% for paper-based picking processes.
30% for pick-to-light (PTL) operations.
35% for radio frequency (RF) scanning systems.
By combining voice picking with warehouse management systems (WMS) or warehouse execution systems (WES), companies can gain real-time visibility into DC performance, optimise picking strategies, and reduce order cycle times. Voice automation also enables companies to prepare for and support growth in the number of SKUs and higher order volumes without adding labour or square footage to the DC.
3. Does your company experience significant turnover and other labour costs?
DCs often experience frequent employee turnover, which drives up costs for onboarding and training. With voice-automated technology, the time required to get new or temporary hires up to speed is reduced; employees become efficient and productive quickly. Improved employee satisfaction and safety also result from voice technology use. In addition, employees can be quickly cross-trained to perform other process workflow tasks integrated with the solution.
4. Is your company experiencing workplace injuries due to distractions?
Voice automation enables employees to work hands-free and eyes-up by removing distractions such as looking down at orders printed on paper or the screens of mobile devices. Employees become more aware of their DC surroundings, including forklift traffic, which can lead to fewer injuries and workplace deaths.
5. Can your company fully comply with inventory control regulations and meet sustainability goals?
Key tracking information required by laws and regulations — e.g., production batches, lot numbers, dates and serial numbers — can be collected and updated with voice technology. This makes compliance consistent and cost-effective.
In addition, companies can advance their efforts toward sustainability by eliminating paper and reducing their reliance on labels. Not only does voice technology lower the expenses for paper, but it also can increase energy efficiency by using fewer printers.
6. Do you wish you had greater visibility of your inventory?
Voice-guided picking can help to optimise inventory management and trigger replenishment processes in real time. The technology provides:
- Frequent or interleaved cycle counting.
- Tracking of storage location moves or transfers.
- Timely identification and replenishment of low-stock or out-of-stock SKUs and damaged goods.
Companies can leverage these insights to reduce safety stock levels and inventory holding costs. In addition, costs for periodic inventory counts can be lowered because voice-equipped employees can check and report inventory levels while performing other tasks.
If you answered YES to any of these questions, then let’s talk.
Schedule a distribution centre workflow audit or demo with a Honeywell process expert below.
Related Campaigns

Expert Insights for the Connected Store and Future Warehouse
Technology plays a vital role in any industry setting.
From the fast-moving nature of a warehouse environment to the competitive world of the retail supply chain, the right innovations deployed with the right solution can have a profound effect on a company’s success.
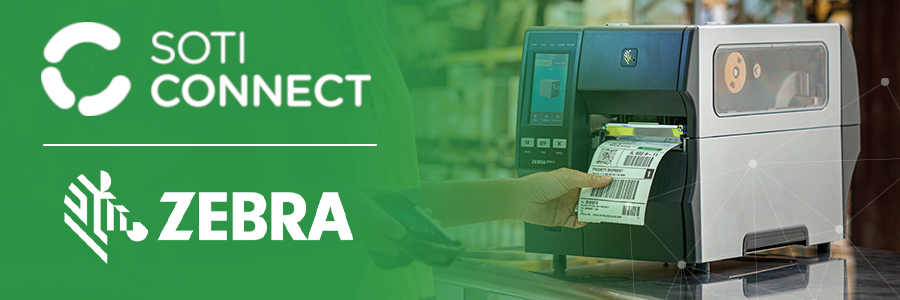
Keep Your Zebra Printers Printing With SOTI Connect Print Management Solution
Your customers operate in complex environments and distributed operations.
They’re constantly moving, and they leverage mobile technology to help them do their jobs.

‘Take Five’ To Focus On In-Store Operational Efficiency
Economic uncertainty and changing priorities in consumer spending mean markets like retail, hospitality and entertainment are all at risk.
Some four out of five (81%*) UK consumers claimed to be reassessing their spend with retail brands this year.