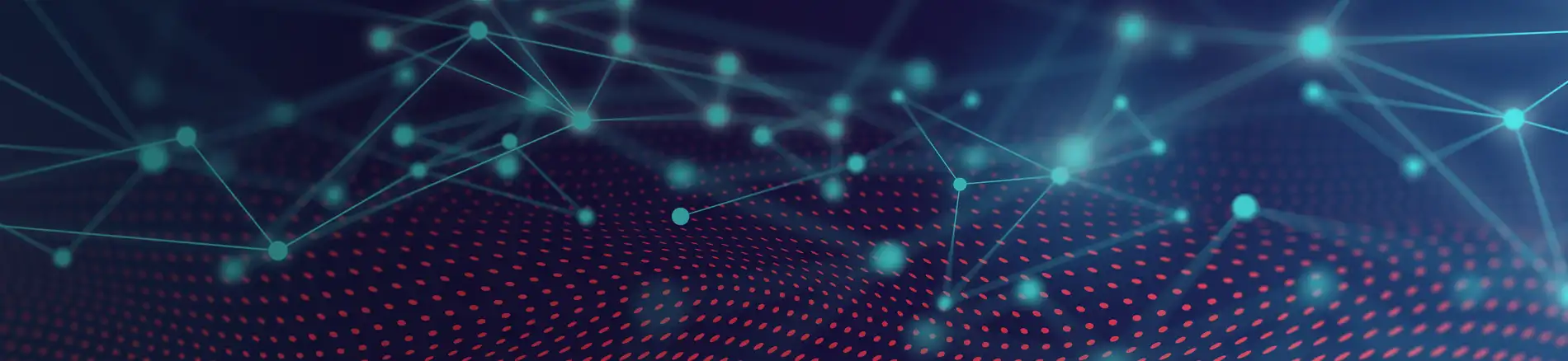

How Robotics and AMRs are Upgrading Warehouse Automation
Over recent years, the widespread adoption of robotics and Autonomous Mobile Robots (AMRs) has transformed the face of warehouse automation.
According to BusinessWire; “Warehouse Automation Market size was valued at USD 19.88 billion in 2022, and is projected to reach USD 54.60 billion by 2030 at a CAGR of 10.9% during the forecast period.” With their ability to perform tasks autonomously, navigate complex environments and collaborate with humans, this cutting-edge technology helps businesses boost efficiency and productivity, optimise the fulfilment process and future-proof their business.
In this article, we’ll be deep diving into what AMRs are, how they’re reshaping the warehouse landscape and why adoption is the path every warehouse should be taking for optimal growth, even in uncertain economic times.
What are Autonomous Mobile Robots (AMRs)?
Autonomous Mobile Robots (AMRs) are machines designed to perform tasks and navigate autonomously without human intervention. Using a combination of advanced sensors, cameras, and software algorithms, they can understand their surroundings, navigate around permanent and temporary obstructions, plot the most efficient path and carry out tasks independently.
AMRs are usually used for warehouse automation, manufacturing facilities and logistics centres. Benefits include enhanced productivity, reduced human error and improved safety. They also help increase scalability when picking orders, transporting goods, managing inventory and handling materials.
AMRs vs AGVs – What’s the difference?
You may have noticed that AMRs hold a striking resemblance to their warehouse-based predecessor, the AGV (or Automated Guided Vehicle). These types of robotics have already been used for several decades for material handling and transportation tasks and can also operate autonomously or semi-autonomously.
However, there are key differences between AMRs and AGV including their navigation technologies, flexibility and adaptability, ability to collaborate with humans, cost and scalability and ease of set-up and integration.
The advantages that AMRs offer mean they’re smarter, faster, more advanced from a hardware and programming perspective, and ultimately more efficient than a traditional AGV unit. Here are a few of the reasons why they’re vital for enhanced warehouse automation operations:
Navigation and guidance
AGVs typically rely on fixed physical infrastructure to navigate around the warehouse premises. This can include magnetic tapes, wires or reflectors that guide them along predetermined paths.
AMRs, on the other hand, offer autonomous navigation, utilising advanced sensors, scanners and software algorithms that allow them to adapt their routes dynamically based on the physical environment.
Flexibility and adaptability
AMRs are more versatile and adaptable than AGVs because they can navigate through a complex environment, handle permanent and temporary obstacles, and adjust their paths in real-time. If they are needed for different tasks, they can be easily programmed or reconfigured according to the needs of the operation.
In contrast, AGVs operate on fixed routes and are designed for specific tasks or applications. This means they’re less flexible when it comes to adapting to changes in the environment or new workflow requirements.
Collaboration with humans
One of the primary advantages of AMRs is their ability to work in collaboration with humans, adjusting their operations and detecting and avoiding obstacles. This allows them to assist humans and ease the physical workload by assisting with repetitive tasks or those that require strength or precision.
AGVs don’t have this ability and usually work in separate areas due to their fixed paths and lack of adaptability.
Implementation and integration
AMRs can be easily and quickly integrated into existing systems and workflows to help support faster deployment without unnecessary disruption. You won’t need to modify your existing environment or waste time implementing this technology but instead can benefit from this technology almost immediately.
On the other hand, AGVs require time and money for setup, implementation, and integration because of their guidance systems. That can include the installation of markets, embedded wires, or other alterations to the physical environment.
Cost and scalability
When it comes to cost, AMRs do require a higher investment than AGVs but demand less in maintenance costs or infrastructure expenses. They’re also more flexible and adaptable, potentially leading to faster return on investment and lower long-term costs.
AGVs are cheaper upfront but may cost more long term when it comes to maintenance and infrastructure expenses. If you want to modify or expand their fixed infrastructure, they require more effort and resources to change.
Using robotics for warehousing automation
AMR robotics can be used for a variety of tasks and processes, enhancing efficiency, accuracy, and productivity. Here are some of our suggestions for deploying robotics in the warehouse and DC:
Order picking and fulfilment
Robotic systems are widely used for order picking as they can navigate through their environment autonomously, speeding up the order fulfilment process, reducing errors and improving customer satisfaction.
Goods transportation and sorting
AMRs can be used to transport goods within the warehouse to designated areas, sort and organise goods based on predefined criteria, optimising space utilisation and streamlining inventory management. This reduces the need for manual labour and makes it easier to handle heavy or bulky items.
Inventory management and tracking
Robotics technology allows you to manage and track your inventory in real-time, using barcode readers, RFID readers or computer vision to scan and identify products, update databases, and trigger restocking or replenishment orders when necessary. This can help reduce errors, improve accuracy, and enable you to make better decisions regarding stock, demand forecasting and order fulfilment.
Warehouse cleaning and maintenance
Whether you want to clean your warehouse or carry out maintenance tasks to ensure a safe working environment, AMRs can help. They can conduct basic repairs, reduce downtime, and optimise equipment performance without extra expense or input from humans.
Collaborative work with humans
AMRs can also be used in collaboration with humans for enhanced warehousing automation, helping with tasks that require strength, precision, or repetitive action. This can reduce strain on workers and improve efficiency.
Quality control and inspection
Using AMRs allows you to automate quality control processes, improving accuracy and consistency while reducing human errors. This includes checking for defects, measuring dimensions, checking packaging, and ensuring compliance with quality standards.
Returns processing
You can reduce time on processing returns when you use AMRs. They assess the condition of returned goods, determine appropriate actions and update inventory systems accordingly. This enables you to streamline your inspection, sorting and repackaging of returns.
Because AMR robotics technology is so flexible and versatile, it can help you promote greater efficiency while also cutting overheads. It can help reduce lead times and help you adapt to the needs of the supply chain.
Summary
Considering the rapid growth of robotics technologies and their myriad benefits, it’s hardly surprising that AMRs are on the rise.
Here at Renovotec, we provide cutting-edge and in-depth knowledge and expertise in warehouse automation. We help optimise your processes by leveraging the right technology for your unique requirements. Contact us today to speak to one of our warehousing and robotics solution experts.
Related Blog Posts

3rd Annual Innovation Forum and Golf Day
Last week saw the highlight of the Renovotec calendar; our 3rd Annual Innovation Forum and Golf Day.
Hosted at Renovotec’s first of its kind Innovation Centre in Newton-Le-Willows, the morning event brought together the Renovotec team, partners and clients to showcase the latest RFID and logistics tech, hear about the latest trends from Industry experts and experience […]
Retail Experts Share Top E-Commerce and Logistics Trends for 2025
Faki Saadi, Director of Sales UKI at SOTI and Richard Gilliard, Managing Director at Renovotec, explore the key trends shaping the future of the retail supply chain From Asda rolling out electronic shelf labels to Amazon launching ‘Prime Air’ a delivery drone service, retail brands are evolving and looking to the latest technologies to keep […]
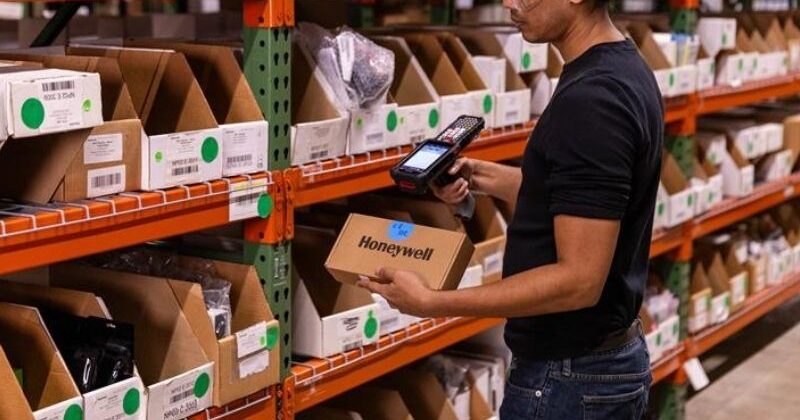
Upgrading the supply chain with Honeywell voice and mobility solutions
How can you transform your supply chain operations and ensure competitiveness in the market with voice and mobility solutions from Renovotec and Honeywell?
Improving productivity and efficiency gains are vital for the profitability of businesses in the supply chain.