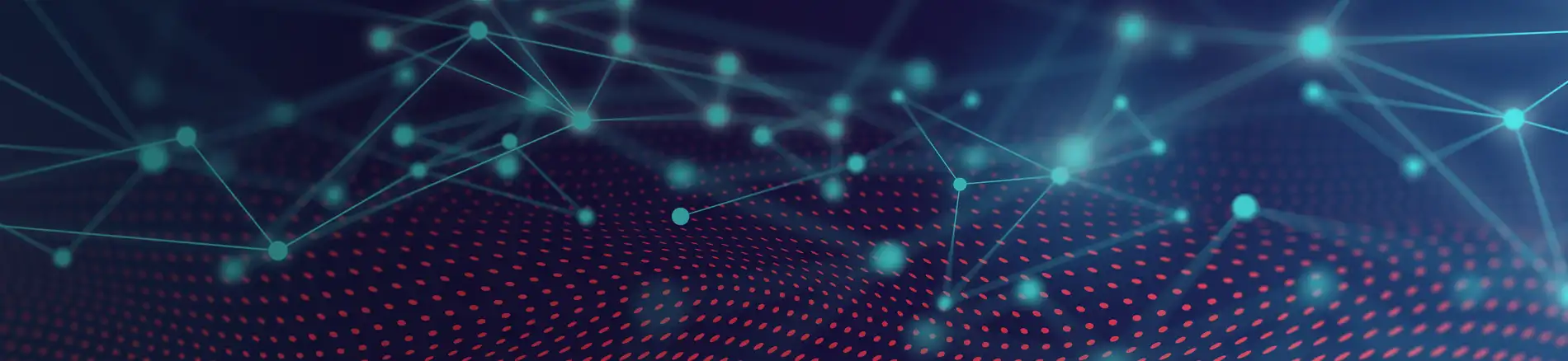

5 Ways Voice Automation Positively Impacts Picking Workflows
Voice automation can have significant and far-reaching impacts. Transforming the most labour-intensive operation within a warehouse to one of the most productive and efficient.
Contact us for further information.
Voice Quiz – Is voice picking a solution for your operation?
Picking is one of the most labour-intensive operations within a warehouse. Thus, making it one of the top supply chain processes to be improved with voice automation. Costly and cumbersome picking methodologies (such as paper and radio frequency [RF]) are prone to errors. As well as taxing on employees and even potentially detrimental to safety.
Outlined below are five ways how voice-automated picking workflows can deliver desired business outcomes.
1. Improve Operational Accuracy
By leveraging a voice-directed, hands-free/eyes-up technology, order error rates will typically be reduced by 50 to 90%, as voice delivers up to 90% improvement over paper-based operations; up to 15% improvement over pick-to-light (PTL) operations; and up to 25% improvement over RF scanning operations. Further, with your orders delivered correctly the first time, incurred costs are avoided in many areas of the value chain. Such as administrative charges, re-picks, re-delivery and cost of lost sales.
2. Increase Worker Productivity
Combining hands-free picking operations with warehouse management system (WMS) or similar software, voice-directed picking delivers productivity improvements that can reach up to 35% for paper based operations; up to 30% for PTL operations; and up to 35% for RF scanning operations. Additionally the solution enhances WMS use by reducing order cycle times throughout a warehouse and optimising its picking processes. Voice automation enables employees to work at peak performance with the elimination of distractions and unnecessary steps. Which is crucial when employees are incentivised and compensated on metrics like pick rate and accuracy.
3. Optimise Staffing for Greater Labour Savings
Many warehouses are plagued by high rates of staff churn and turnover. While the labour market remains incredibly competitive. With the inherent voice-driven nature of the solution, training and onboarding times are reduced for cross-training, new hires and temporary employees. It also supports incentive programs and expands the pool of potential workers. Providing multilingual capabilities that cover more than 50 different languages and dialects.
4. Enable Analytics for Continuous Improvement
Analytics of data and transactions generated by voice-automated picking systems provide a means to achieve continuous productivity gains. This analysis can help managers to determine when to move workers from one zone to another based on workflows. Or spot patterns that can help to fine-tune performance. It further identifies when the system should be adjusted to adapt to a worker’s picking speed, enhancing productivity.
5. Support Greater Operational Agility to Meet Consumer Demands
Voice technology supports warehouse optimisation software — which guides the optimal placement of goods given current demand — by providing real-time visibility and direction to workers. As warehouse optimisation software determines the most efficient picking routes and pick strategies, handles replenishment and inventory control, and interleaves staff tasks. So that voice-directed employees can continue to follow voice directions. Even as operational strategies change.
Contact us for further information.
Why Honeywell?
Honeywell’s voice automation solutions are designed to free mobile workers’ hands and eyes to maximise productivity, reduce inefficiencies, and achieve higher accuracy rates. Their robust solutions are comprised of:
- Rugged, noise-cancelling headsets with SoundSense™ technology.
- Directional microphones that deliver clear, crisp audio from your workers into the system.
- Optional headset configurations, which enable use with a regular headband, a cupped headband or a hard hat.
- A wearable mobile device to interface with the Honeywell Voice system.
- Advanced software to integrate with your preferred host system.
Related Campaigns

Expert Insights for the Connected Store and Future Warehouse
Technology plays a vital role in any industry setting.
From the fast-moving nature of a warehouse environment to the competitive world of the retail supply chain, the right innovations deployed with the right solution can have a profound effect on a company’s success.
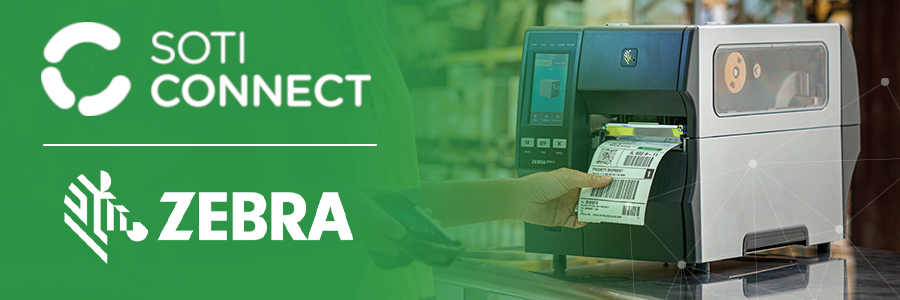
Keep Your Zebra Printers Printing With SOTI Connect Print Management Solution
Your customers operate in complex environments and distributed operations.
They’re constantly moving, and they leverage mobile technology to help them do their jobs.

‘Take Five’ To Focus On In-Store Operational Efficiency
Economic uncertainty and changing priorities in consumer spending mean markets like retail, hospitality and entertainment are all at risk.
Some four out of five (81%*) UK consumers claimed to be reassessing their spend with retail brands this year.