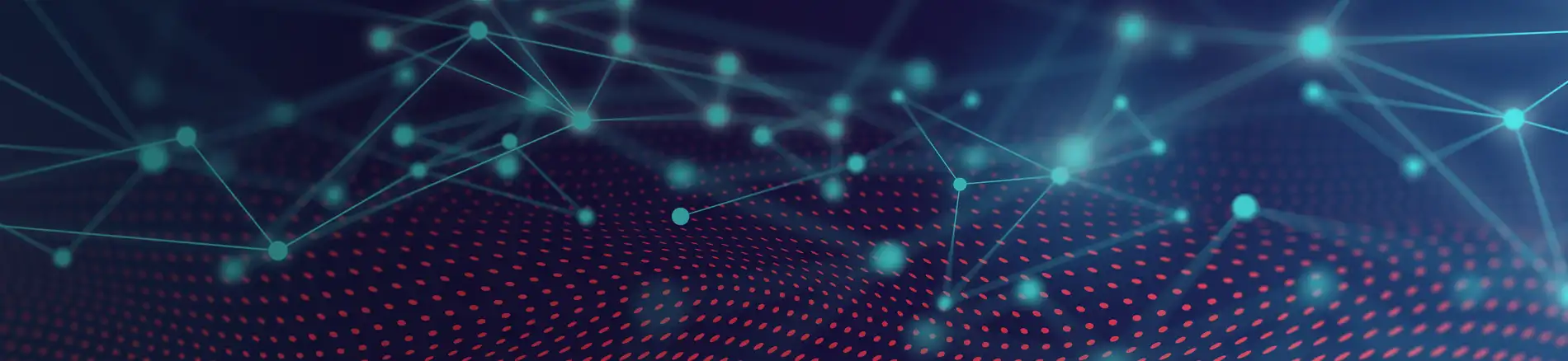

What is Voice Picking for the Supply Chain?
Voice picking technologies for the supply train use voice recognition to help warehouse pickers complete their tasks quickly, effectively and with increased accuracy.
‘Paper-free’, ‘hands-free’ and ‘eye-free’, they are simple and intuitive to use and allow the picker to move through all stages of order fulfilment with greater confidence.
For this reason, voice picking technologies are ideal for use in the 21st-century supply chain. Especially for warehouses and distribution centres (DCs). In fact, Data Bridge Market Research says that this technology is likely to grow by 15.1% over the next five years. Potentially becoming the industry standard for the era of automation and data.
How does a voice picking system work?
A voice picking system for warehouses usually takes the form of a compact and comfortable headset. Often linked to a wearable device or a ring scanner.
Using the speech-recognition technology, the pickers receive data directly from the WMS (Warehouse Management System) or ERP (Enterprise Resource Planning) system via a series of audio prompts. Which they then confirm with their own voice.
Here is how it works in a little more detail:
1. Associate set-up
Warehouse operators receive their headset, mobile device or voice dedicated terminal. (Sometimes in conjunction with a wrist-mounted terminal and/or a ring scanner.) After that minimal training is required and only a voice template is needed. Which can be created in less than an hour. Since everything is done via voice commands, a worker won’t need additional training on reading labels, etc. Hence, the technology can be deployed into the workplace much faster.
2. Picking tasks distributed to workers
Utilising data directly from the WMS or ERP, a voice picking technology solution then organises and creates work assignments/tasks. Before distributing them directly to the order pickers via their respective headset.
3. The worker receives their instructions
Immediately, the worker will receive a voice message on their headset that defines exactly where they need to go, what SKU to pick and how many are needed.
If they have a query, they can ask the system itself to clarify, both quickly and easily.
4. The worker carries out the order picking task
Once the worker understands the task, they can move directly to the picking location, say the control code into the microphone and pick the item and quantity required. Before finally confirming the action to the system.
5. The system verifies the operation
The WMS or ERP will then receive the information and check the amount of stock remaining to ensure the correct quantity has been picked. If it is satisfied it will mark the task as complete. Before issuing the next picking request. If not, it will highlight the problem and tell the worker how to rectify the problem.
6. The worker can move on to the next task
Once the system is happy, it will send the picker to the next location. Optimising pick paths to increase productivity and efficiency. All interactions between the voice application and the operator themselves are tracked in real time. So the warehouse director or manager can view the progress of orders.
What warehouse tasks can voice picking be used for?
This cutting-edge voice-activated technology can also be used for other warehouse tasks. Not only controlling the order fulfilment process. This includes any other process that involves moving inventory or workers performing a task where a more hands-free approach would be of greater benefit. Such as:
- Cross-docking: The voice-directed warehousing system can help operators unload products from a lorry. Sort out individual items. And, then prepare them for outbound transport.
- Pick by line: Disassembling arriving pallets is made easy thanks to the instructions that this voice technology can send.
- Picking to conveyor: Using the same technology as warehouse picking, the voice commands can guide the worker to pick the required number of cases and then place them onto the correct outbound conveyor.
- Packing and consolidation: Voice picking can also be used to help assemble multiple line orders. That will then be picked in different zones or batches.
- Inventory management: Inventory management is made easier and faster thanks to this highly accurate voice-directed technology.
- Receiving and returns: When workers use voice picking alongside barcode scanning and visual display, they can quickly and easily verify the quantity, identify damage and receive mixed pallets or items more quickly and easily.
- Putaway: This technology can also be used to help warehouse operators replenish items and remove them from bulk storage to forward picking locations.
- Quality control and audit: These intelligent voice solutions can help streamline the warehouse evaluation process including quality checks and audits. They can set parameters such as customers and product type and use this information to guide their business decisions moving forward.
What are the benefits of a voice-activated picking system?
The simple and intuitive system is totally hands-free which means the worker doesn’t need to read, scan, write down details and can simply speak normally when carrying out their tasks. It also features a range of reporting and management tools that can help improve accuracy, remove unnecessary costs and streamline the warehouse operations processes.
Here are some more of the benefits you can leverage with the power of voice:
- Boosts speed and accuracy: Voice picking frees up the workers’ hands and eyes. Thus offering freedom of movement and a wider field of vision so they can pick the right item and the right quantity faster and with greater accuracy.
- Enhanced productivity: With these enhanced tools in use, workers will become more efficient, avoid distractions and boost overall productivity.
- Fewer picking errors: Using voice picking, the worker can focus on the task at hand and avoid making mistakes or encountering setbacks that can cost the business precious time and money.
- Increased inventory accuracy: The accuracy of voice picking and the ability to optimise multiple warehousing processes means that businesses can manage their inventory more accurately.
- Safer warehousing: Workers have their hands free when using voice activated technologies. And, can spot potential risks and bolster health and safety standards.
- Shortens training time: Voice tech requires very little training because it uses simple, user-friendly voice commands to guide the worker through their tasks. This means new employees can be skilled up and working in less time than with traditional methods.
- Fast ROI: Voice picking offers a faster return on investment than many other forms of warehouse automation. As it’s affordable, straightforward and can vastly improve warehouse processes at every stage of the fulfilment process.
Could voice-picking technology help streamline your warehouse operations?
Every warehouse manager knows that optimising the order fulfilment process is key to driving the future success of the business. This means adopting these cutting-edge tools to ensure that operations are cost-effective and efficient as possible.
With voice picking technology for your warehouse, you could tick all these boxes in an affordable way without having to invest hours in retraining and gain a faster ROI that supports increased growth. It also offers countless application opportunities. Including transforming your maintenance and inspection procedures.
Renovotec has years of experience supporting customers with voice-directed solutions, and our experts are ready to help build an end-to-end solution that transforms your warehouse operations with the power of voice.
Want to learn more about voice picking for your warehouse or organisation? Contact us today.
Related Blog Posts

3rd Annual Innovation Forum and Golf Day
Last week saw the highlight of the Renovotec calendar; our 3rd Annual Innovation Forum and Golf Day.
Hosted at Renovotec’s first of its kind Innovation Centre in Newton-Le-Willows, the morning event brought together the Renovotec team, partners and clients to showcase the latest RFID and logistics tech, hear about the latest trends from Industry experts and experience […]
Retail Experts Share Top E-Commerce and Logistics Trends for 2025
Faki Saadi, Director of Sales UKI at SOTI and Richard Gilliard, Managing Director at Renovotec, explore the key trends shaping the future of the retail supply chain From Asda rolling out electronic shelf labels to Amazon launching ‘Prime Air’ a delivery drone service, retail brands are evolving and looking to the latest technologies to keep […]
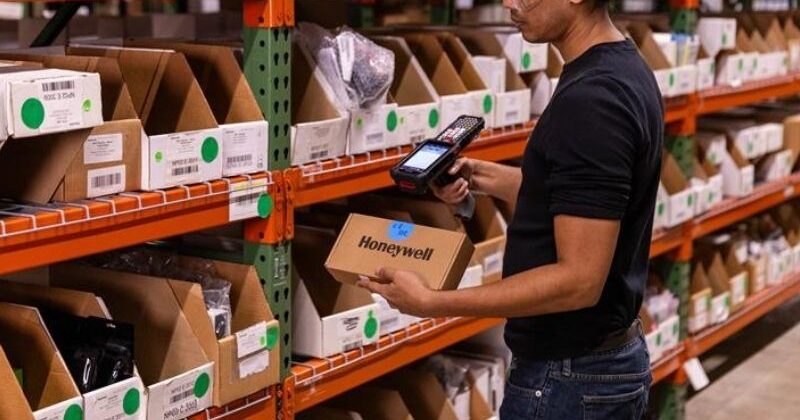
Upgrading the supply chain with Honeywell voice and mobility solutions
How can you transform your supply chain operations and ensure competitiveness in the market with voice and mobility solutions from Renovotec and Honeywell?
Improving productivity and efficiency gains are vital for the profitability of businesses in the supply chain.