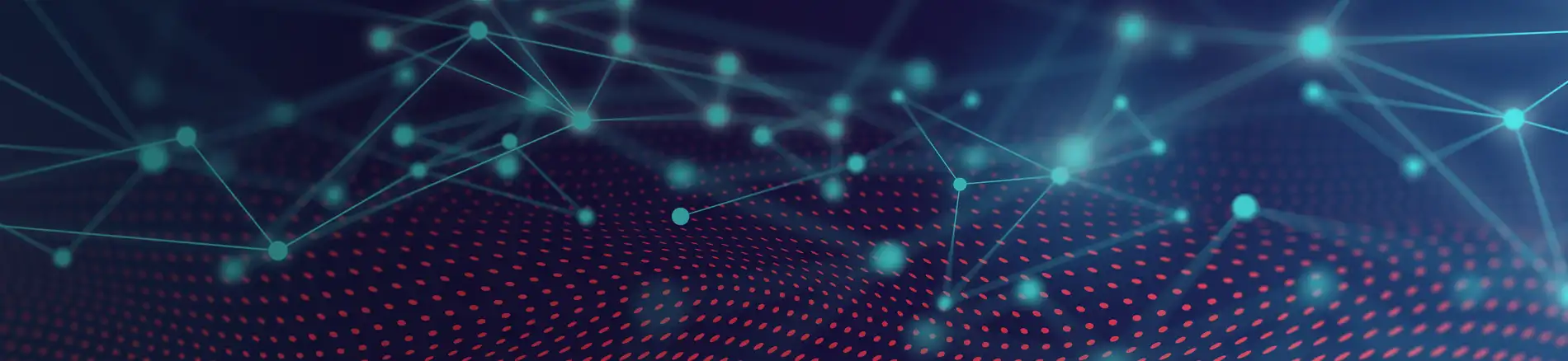

Warehouse workflows; counting the cost of errors
What are the primary mistakes made with warehouse workflows?
Ecommerce continues to boom after unprecedented online retail sales created by Covid-19 lockdowns. This inevitably put a strain on transport and logistics (T&L). Which faced the added difficulties of adapting to new health and safety requirements while trying to fulfil orders.
And since the pandemic started, customers have become decidedly more demanding. Tracking is no longer a ‘nice-to-have’. Many (86%*) deem it important or very important. Over half (56%*) evaluate delivery choice when shopping online and nearly a third (32%*) value sustainability over cost and speed. That’s a lot of demands. With 81%* of consumers reporting a negative experience in the past 12 months, there is clearly plenty of work to be done both in distribution centres (DC) and in the last mile.
Honeywell’s Report
In its report ‘When retail and logistics converge’, Honeywell claims the shift in buying behaviour means the traditional approach of analysing these markets as two separate entities no longer applies. It suggested that without omnichannel strategies and fluid, reliable technologies and processes, many retailers could get left behind.
Before Covid changed the world forever, Honeywell produced a report on hidden costs in the DC. In which it revealed that companies suffered around 134† mispicks per week. Thus, costing them some £324,000† a year. It also discovered that 3,000 hours are lost annually in DCs on inefficient processes. Such levels of inefficiency and cost to the business are unsustainable, a point implicitly acknowledged by 89%† of managers who believed that investing in new technology would enable them to achieve savings and improve worker productivity.
But not all businesses can afford the capital expenditure of new printers, scanners and mobile computers. Which is why Renovotec Rentals could prove advantageous in either providing the latest hardware to cover spikes in demand, or for phasing in Android devices.
However, for technology to have a positive impact on productivity, it must be coupled with good processes. If, for example, you implement a new system but still rely on poor methods and procedures, or paper (23%† of DCs do) then you’re unlikely to reap the full benefits of your investment.
When paper trails are analysed it is often single picks that prove less efficient. DCs try to use paper or RF instead of implementing workflow technologies like handhelds, wearables, voice or mobile printers. Indeed, it is these devices that add an incremental layer of accuracy and productivity that operations will not get from traditional paper-based systems.
Barcode Scanners
Take Honeywell’s Granit 1990iXR & 1991iXR expanded range scanners. Trying to read damaged or low-quality barcodes in DCs can create bottlenecks. But Honeywell’s Granit devices use its next generation imaging platform with high-resolution sensors and enhanced decoding algorithms. That can quickly and accurately scan and transmit barcode symbols and keep transactions flowing. They can read UPCs from 1.5 metres away and rack labels from 10 metres.
DCs also need to consider error rates at both goods in and out when assessing productivity. When handled incorrectly, the receiving process can have rippling effects across the supply chain. If orders are correctly received, inventory balances are updated, new orders are generated and fulfilled according to those inventories and filled rates are high. It only takes one of those processes to go awry before orders are fulfilled incorrectly, dispatches are delayed and customers negatively impacted.
With the T&L sector facing ever smaller orders and shrinking delivery timeframes, it desperately needs ways to improve inventory accuracy and order cycle times. Honeywell’s CK65 ultra-rugged mobile computer is purpose-built to help achieve these objectives and maximise worker productivity. Its extended battery life means it’s also capable of working 28 hours straight, so no dead batteries on its watch!
Errors aren’t just made at the receiving end, they can also happen when least expected. Badly printed/difficult-to-scan barcode labels, for example, can cost firms dearly in fines, chargebacks, reputations and even lawsuits! Honeywell’s PX940 precision printer produces error-free labels every time. Its integrated label verification technology checks the accuracy of every label in real-time. If it finds one not meeting the standard, it voids it, reprints a new one and reports the error. And with registration capabilities up to +/-0.2mm, it’s perfect for the trend towards miniaturised labels.
Conclusion
With the sheer velocity of orders moving through warehouses and DCs, organisations either have to take on more space and workers – both costly endeavours – or optimise their operations and do more in the same space with the same staff numbers. Don’t wait for non-compliance, poor performance or customer complaints (16%†) to prompt a review of your processes. It may prove too little, too late.
Renovotec Rentals can provide the latest hardware you need and preserve your company capital. Its managed print service (MPS) could also audit your existing printer assets, maintain or replace them, provide on-going performance reporting on them as well as ensure you never run out of media and consumables.
Footnotes
*Source: Ten retail and leisure trends for 2021, NatWest and Retail Economics.
† Source: ‘Unlocking hidden cost in the distribution centre’, Honeywell.
Related Campaigns

Expert Insights for the Connected Store and Future Warehouse
Technology plays a vital role in any industry setting.
From the fast-moving nature of a warehouse environment to the competitive world of the retail supply chain, the right innovations deployed with the right solution can have a profound effect on a company’s success.
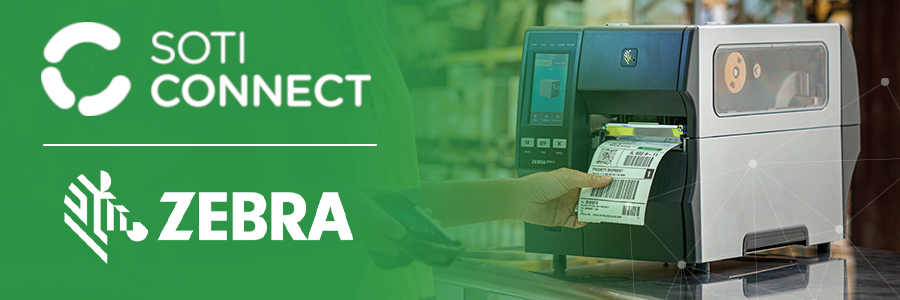
Keep Your Zebra Printers Printing With SOTI Connect Print Management Solution
Your customers operate in complex environments and distributed operations.
They’re constantly moving, and they leverage mobile technology to help them do their jobs.

‘Take Five’ To Focus On In-Store Operational Efficiency
Economic uncertainty and changing priorities in consumer spending mean markets like retail, hospitality and entertainment are all at risk.
Some four out of five (81%*) UK consumers claimed to be reassessing their spend with retail brands this year.