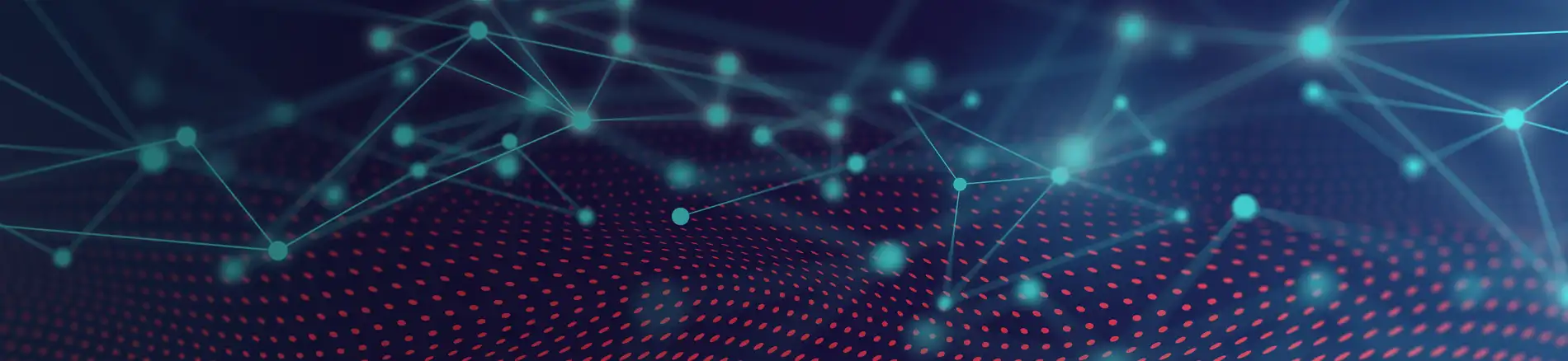

Not All Voice Solutions are the Same: How Small Changes Can Make Big Supply Chain Impacts
Every organisation is different. Even in a market with similar customer demands and familiar challenges, businesses in the supply chain and retail sector are still unique in how they approach those challenges and meet customer expectations.
That’s why ‘off the shelf’ solutions often fall short of the mark. Deploying a standardised set of technologies onto a warehouse floor or into a retail environment isn’t directly addressing the issues that are affecting the speed, accuracy and productivity of that business setting.
Voice-directed technology is a proven technology in these markets, but not every solution fits every problem. When you consider the challenges facing the supply chain – including labour shortages, increasing customer demands, seasonal peaks in business and sustainability concerns – it’s clear businesses need custom solutions that address these obstacles.
In this article from Renovotec, we’ll explore how developing a voice solution that’s tailored to the unique aspects of a warehouse or retail store can drastically improve KPIs and deliver outstanding ROI.
Simplifying needlessly complex processes
As businesses grow, so does the complexity of their operations. With that comes more convoluted processes and managers and workers attempt to cope with increased customer demand. Thankfully, voice can help relieve much of this pressure by introducing voice-enhanced workflows that integrate directly with existing systems.
Whether a business is using a recognisable warehouse management system (WMS) / warehouse execution system (WES), or something developed in-house, a voice solution specialist can work with management and IT teams to integrate voice into these existing systems as well as introducing new and optimised workflows.
An effective voice solution will go beyond its core elements. It should offer a true ‘eyes and hands free’ experience, but one that considers all other options (such as support for barcode scanning). It should provide instructions and prompts, but with specific information to ensure workers are clearly informed. And recognition that reduces the number of words required while accommodating workflows for both new starts and experienced staff.
With the right application of voice, users can achieve a complete overhaul in order accuracy rates, reduce attrition rate by 30%, improve worker safety by up to 20% and apply significant improvements to specific processes, such as correcting up to 80% of errors found in the picking process. Technology solutions partners with voice experience can work with management and IT teams to develop custom solutions that remove unnecessary manual steps and create a faster, more effective operation.
Unlocking operational potential
In the competitive supply chain and retail markets, any form of operational improvement can grant powerful business advantages. According to a recent report by voice technology specialist and Renovotec partner Honeywell, organisations can potentially increase productivity by 30% by deploying a voice solution into their day-to-day operations.
Voice is a proven technology that continues to evolve to meet the demands of the modern supply chain and retail sector. Data is the lifeblood of any operation in these markets, and voice has the power to gather key data from your daily fulfilment operations.
For an increasingly automated industry, being able to collect and analyse worker performance data, error rates and task completion times gives managers and operations directors the ability to see in real-time where bottle necks are forming in the workflow. Being able to access this kind of data is invaluable in making informed decisions, especially when forecasting for peak periods.
Customisation is one area that also makes voice so flexible. Voice solutions are usually developed to be agnostic of other systems or hardware, so you can pair them with headsets, wearables, mobile computers, barcode scanners and other technology deployed in a warehouse or retail store without the fear of incompatibility. Whether a business is still using older Windows devices or Android Enterprise, voice-directed solutions are highly customisable for any business setup.
Embracing the power of voice
Voice offers potential improvements and productivity gains in a variety of applications. Not only do voice solutions help reduce errors through voice-guided workflows, but they can also be adapted to fit the requirements of any organisation. It’s not just a tool solely designed for picking, it can also be deployed for vehicle and equipment inspections, removing the need to rely on paper checklists or even input observations into a mobile computer.
Retail staff can use voice to perform quality checks on stock and displays on the shop floor or use prompts for product lookups and stock availability. Voice can even be used in retail stock rooms or warehouses at the goods in / goods out point for easier processing of pallets moving in and out of the premises. Other areas that voice can make significant impacts include vehicle inspections / maintenance, cycle counts, replenishments, putaway, returns and much more.
Voice is a proven enabler for change, allowing organisations to make seemingly small adjustments that can have potentially huge impacts on the effectiveness of a fulfilment or retail operation. The power of speech can unlock gains across a business, especially when paired with the latest innovations in rugged mobile computers, headsets and warehouse management systems such as Manhattan Active WM.
Empowering an ever-changing workforce
For many businesses, new technologies often present friction for the workforce, with additional layers of training to effectively roll these devices and systems into an established workflow. Voice, however, is designed for rapid deployment across large and potentially diverse workforces with a minimum of training.
Onboarding staff is fast, easy and far less time intensive than other technologies often in use in on the warehouse floor or a retail store. It’s also ideal for temporary employees, cross-trained associates and non-native speakers. Many voice solutions have extended the languages supported on their platforms, with Honeywell Voice currently accommodating over 40 different native dialects.
Recent innovations in voice recognition are also adding greater functionality to the platform and further enhancing the user experience (UX). Voice solutions now can adapt to individual speech preferences, which helps reduce the need for workers to repeat commands and any loss of productivity those actions would cause. Being able to remove language barriers also helps foster a more cohesive and effective workforce, regardless of how diverse or complex an organisation may be.
It’s not one size fits all when it comes to voice
Voice might be a long-established technology for retail and the supply chain, but it’s far from a stagnant one. New innovations such as improved voice recognition and enhanced data collection are helping organisations in these markets unlock new gain in productivity while reducing error rates.
It’s a technology that’s also proving it can do more than just transform picking efficiency and accuracy rates. It greatly improves the speed and productivity of other key tasks within a workflow such as quality control inspections, inventory and stock management, click and collect processing and much more.
Want to find out how voice can make a positive change to your workflow? Contact our experts in your region and let’s discuss how Renovotec can help. You can also visit Renovotec at the Manhattan APAC Exchange on 29 August 2024 in Melbourne, Australia.
Related Blog Posts

3rd Annual Innovation Forum and Golf Day
Last week saw the highlight of the Renovotec calendar; our 3rd Annual Innovation Forum and Golf Day.
Hosted at Renovotec’s first of its kind Innovation Centre in Newton-Le-Willows, the morning event brought together the Renovotec team, partners and clients to showcase the latest RFID and logistics tech, hear about the latest trends from Industry experts and experience […]
Retail Experts Share Top E-Commerce and Logistics Trends for 2025
Faki Saadi, Director of Sales UKI at SOTI and Richard Gilliard, Managing Director at Renovotec, explore the key trends shaping the future of the retail supply chain From Asda rolling out electronic shelf labels to Amazon launching ‘Prime Air’ a delivery drone service, retail brands are evolving and looking to the latest technologies to keep […]
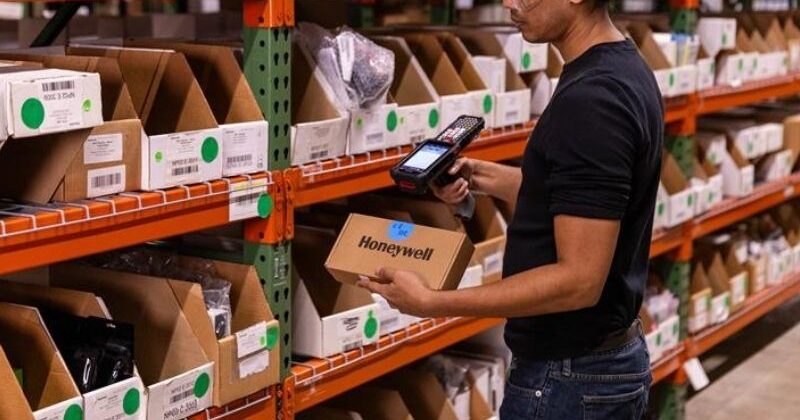
Upgrading the supply chain with Honeywell voice and mobility solutions
How can you transform your supply chain operations and ensure competitiveness in the market with voice and mobility solutions from Renovotec and Honeywell?
Improving productivity and efficiency gains are vital for the profitability of businesses in the supply chain.